Urban, market-rate housing that lower-income workers can actually afford is one of our country’s biggest needs. For multifamily designers, this challenge presents several opportunities for creating housing that workers such as entry-level teachers can afford on their salaries.
Three promising strategies are modular construction, adaptive reuse, and micro-units.
Multifamily Modular Construction Criteria for ROI
This is one of the most exciting evolutions in housing. We have studied modular construction and prefabricated panels/assemblies for more than 20 years, integrating them into multifamily projects whenever viable. Our three criteria for assessing modular’s ROI viability for a project:
- Design Flexibility
- Project Location
- Scale
1. Design Flexibility
One misconception about modular construction is that design choices are made strictly by factory-affiliated designers so that the individual modules will fit on a flatbed for truck delivery. Within that restriction, we’ve found surprising latitude working with modular manufacturers to customize the design to fit the local context and job-site configuration. Modular manufacturers are generally open to design input on floorplans, materials, appliances, and more.
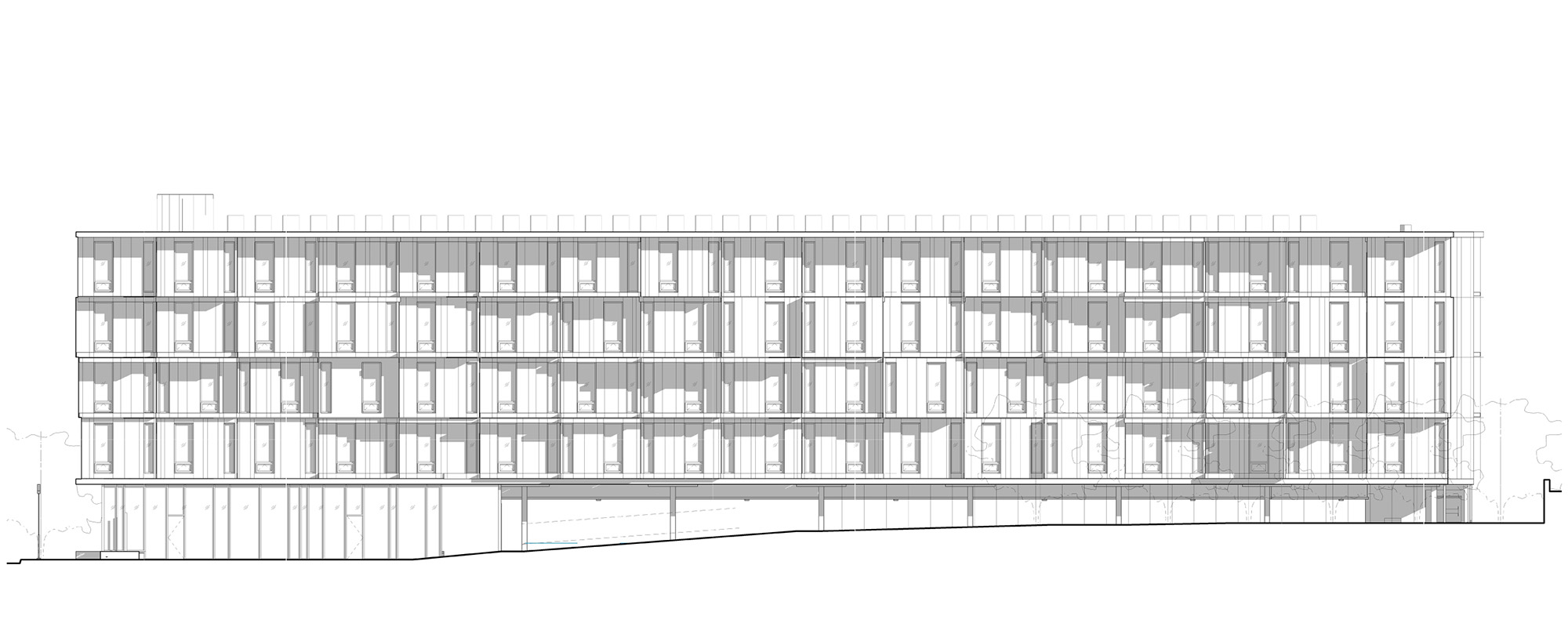
While initial design conversations often discuss downplaying and obscuring the process, we prefer to lean into modular’s building-block bones. As Lego fans, like many AEC professionals, we celebrate the stacked-and-stitched approach to these projects. Realization can include staggering certain modules to accentuate the individual pieces. Further, prefabricated exterior panels and assemblies elevate the assembly-line panache.
2. Project Location
The site has enormous impact on a project’s suitability for modular construction. So that delivery costs don’t negate modular’s advantages over traditional stick-built construction, the site should ideally be within a day’s drive of a suitable factory—generally 400 miles or less, pending topography, population density/traffic, weather, and other variables. Further, rectangular parcels, even narrow infill ones, are well suited to modular construction.
3. Scale
Size of the project is the third determining factor. Under present modular manufacturing capabilities, we feel that 350 apartment units is the upper limit for factory-built modules to be delivered on a financing-viable timeline. Manufacturing capacity should increase in the near future as capital investment accelerates both the number and plant sizes of factories throughout the country. Several states now offer economic stimulus programs that encourage modular manufacturing and project development.
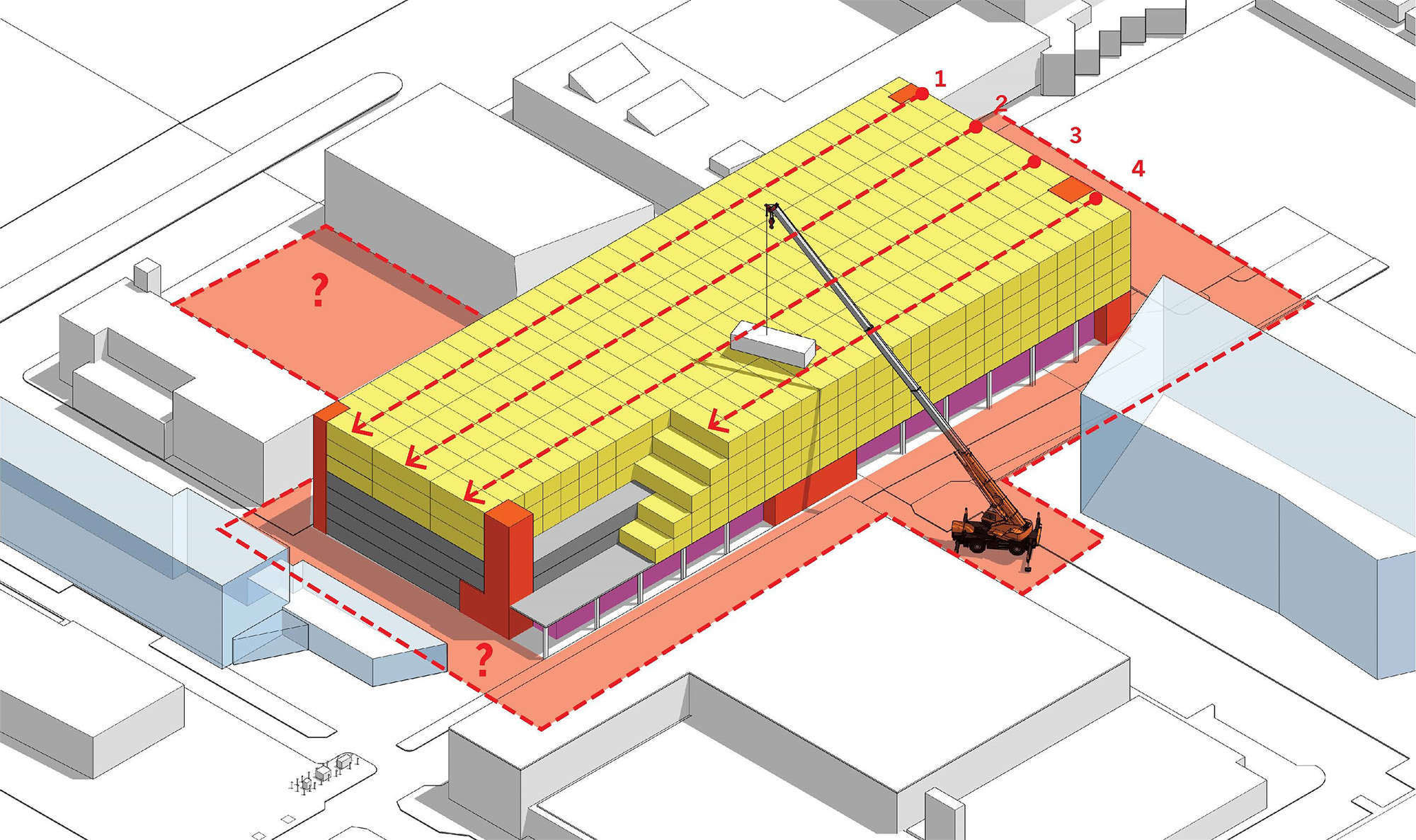
Housing Shortage Solutions with Modular and Prefab
We see modular as an emerging solution for the housing shortage in three primary areas:
Affordable Housing
Since these projects take considerably longer to navigate the layers of government regulations than market-rate projects, modular can save build time for smaller affordable housing projects. As modular manufacturing competition and capacities increase, build costs could conceivably be more advantageous than budgets for stick-built projects.
Missing Middle
Modular construction can accelerate development of market-responsive apartments. Compressing project timelines and saving costs will motivate developers to profitably do projects that rent to tenants earning entry-level wages.
Student Housing
Colleges often have fewer entitlement restrictions than market-rate housing. Modular construction offers college administrators more options for efficiently expanding student housing. On-campus housing design influences enrollment decisions, and studies show that students who live on campus have higher GPAs and better mental health.
Modular Construction Advantages and Disadvantages
The modular construction process has several advantages:
Time
Traditionally, construction financing drives the project timeline. When all stakeholders are organized and aligned, modular can save significant time compared to traditional construction—we currently estimate about 30% faster. Inspections are expedited. Modular manufacturers build the pods to comply with relevant codes, and regular assembly-line inspections ensure compliance.
Scheduling and coordination among all stakeholders are crucial to project success. The ultimate goal is to schedule module delivery to begin as soon as the site is ready; storage costs for completed modules can undermine modular’s advantages. Preliminaries—where a modular-literate architect can be invaluable—include finalizing the design, working with the factory to include materials, and selecting FF&E readily available in the current supply chain.
Construction
Site construction is dramatically simplified. Once the pods arrive at the build-ready site, the modules are placed and connected. Change orders and subcontractors are minimized. Further, module assembly requires smaller crews. This is a huge advantage under the current labor shortage, and smaller crews equate to fewer workers’ comp claims. We’ve found that working with a builder who’s previously done modular projects eliminates what can be a considerable learning curve.
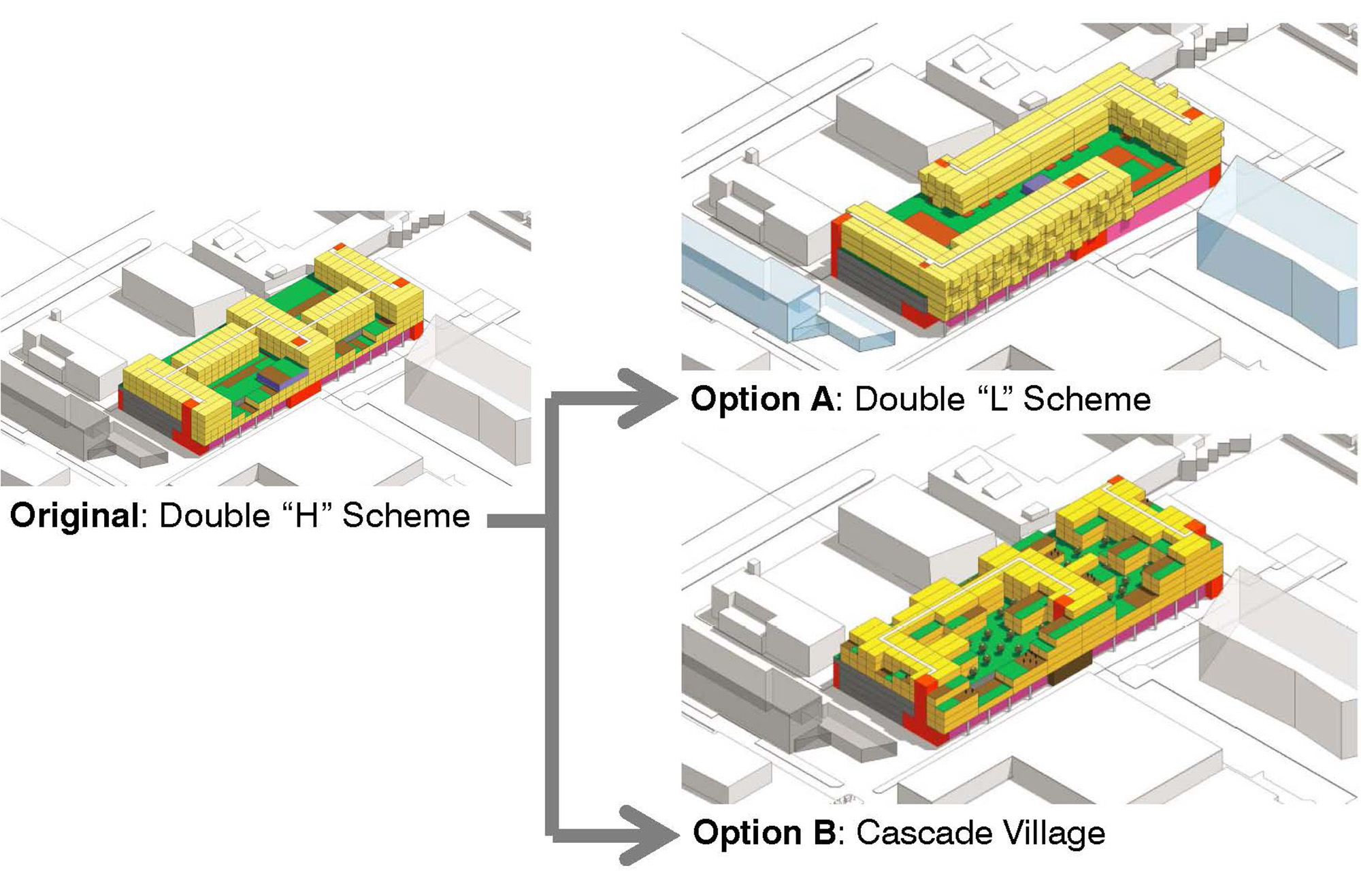
Quality
Automated manufacturing minimizes human error. Quality control is also higher in a factory than on a job site. Even better, each module is wrapped in insulation. This improves thermal performance and sound absorption over traditional construction. One-inch airspace between assembled modules further elevates R-value and increases sound isolation.
Sustainability
Because factory assembly is tightly controlled, materials can be accurately ordered for each project. This minimizes build waste to about 3% for what amounts to approximately 70% of the project’s overall construction. Landfill waste is significantly reduced.
There is one main challenge:
Financing
Financing must be front loaded. In the pro forma, developers must account for large spikes in deposits to the modular manufacturer for ordering materials, finishes, and appliances as a precursor to setting up the assembly line. Lenders can be an obstacle here, as most are accustomed to smaller deposits spread out during the process for stick-built construction. Once banks understand and embrace modular’s shorter loan durations, they will be more enthusiastic. In effect, the overall project timeline is recalibrated, yet is still driven by the construction loan.
Adaptive Reuse, Micro-Units for Residential Conversions
With demand for commercial office space plummeting since the pandemic, landlords are desperate to increase occupancy of existing—and sometimes brand-new—buildings. Residential conversions are a popular topic among politicians. We assess conversion viability on three factors:
- Floor plate
- Condition of the existing mechanical system
- Building envelope
Rectangular floor plates lend themselves to apartment configuration. Odd-shaped buildings do not convert into expected apartment configurations. However, a few oddly shaped spaces can be more viable as community amenities.
In some buildings, updating and upgrading MEP systems for beyond workday demands can be cost-prohibitive. Similarly, the existing envelope can increase MEP load. Lack of operable windows is one example common in buildings from the 1970s.
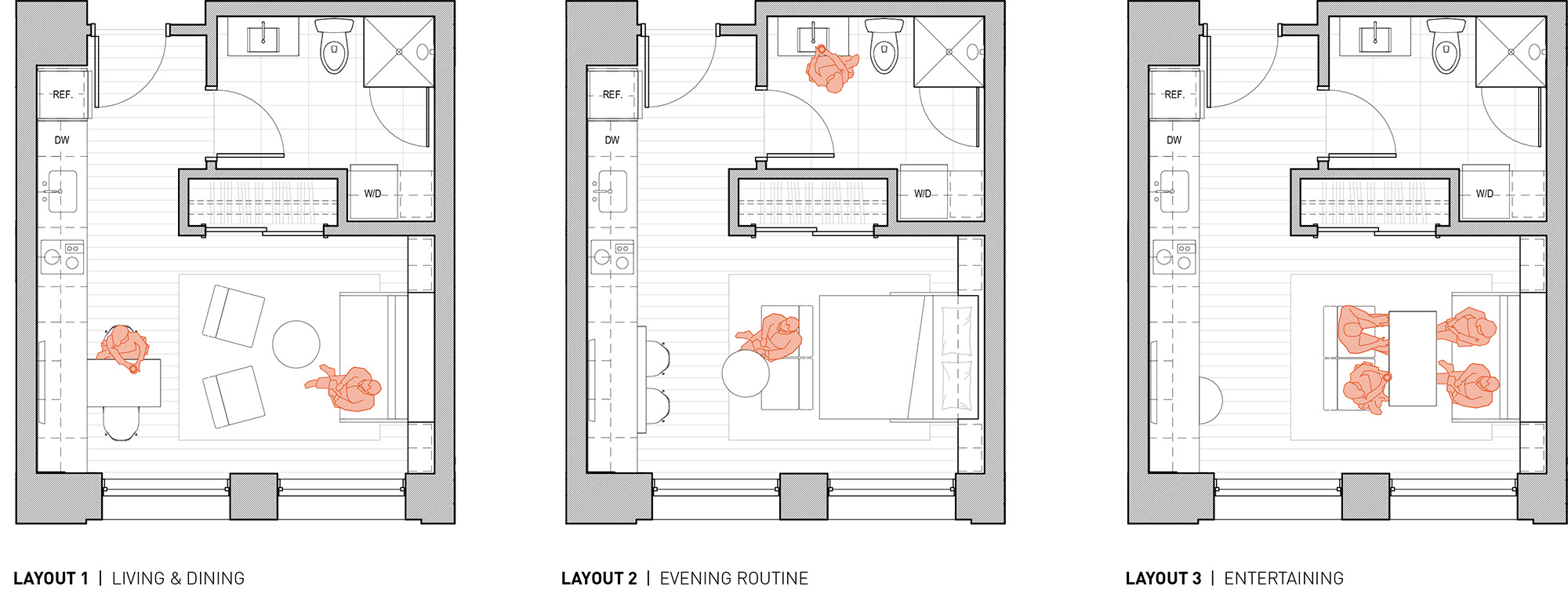
A recent project that combines adaptive reuse of an office building is Midland Lofts in downtown Kansas City. Developer Cordish Company challenged us to transform a long-vacant 1926 Historic Register-listed building whose previous tenants include AMC Theater’s corporate offices into attainable apartments. Cordish identified a local need for monthly rents beginning at about $700 and will select a deserving city employee to receive a year’s free rent at Midland Lofts.
Our initial design fit 117 apartments. Upon further review, we squeezed in 139 units, with studios ranging between about 320 and 470 sf. Odd-shaped niches house amenity spaces, such as a music room/studio and yoga area. Additional communal amenities of a commercial kitchen and co-working lounge supplement the micro-unit apartments. Design inspiration came from the historic Midland Theater, still thriving in the non-tower portion of the building.
Multifamily’s future is encouraging. Micro-unit apartments and modular construction are two design solutions aimed at improving affordability and sustainability.
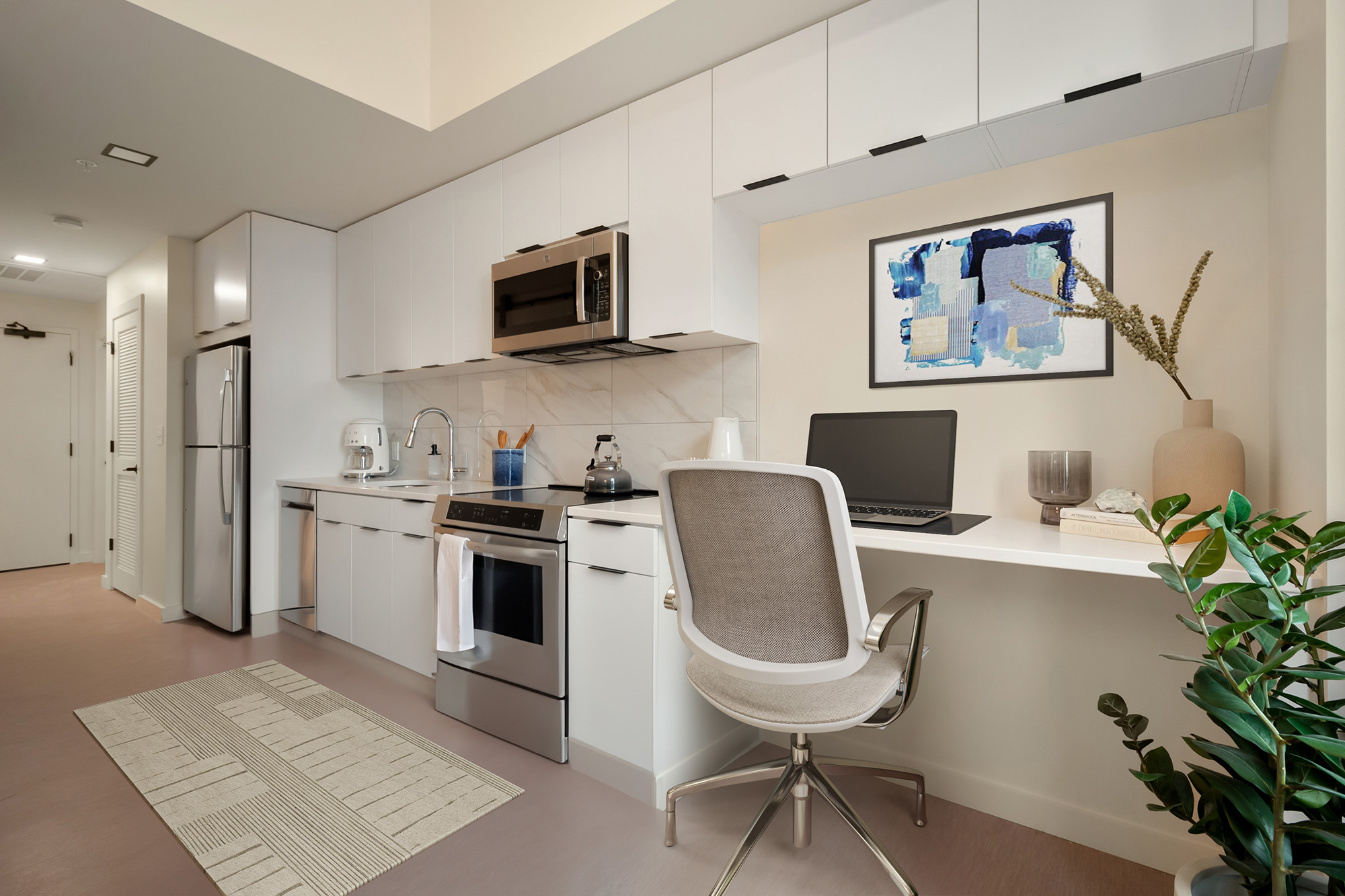
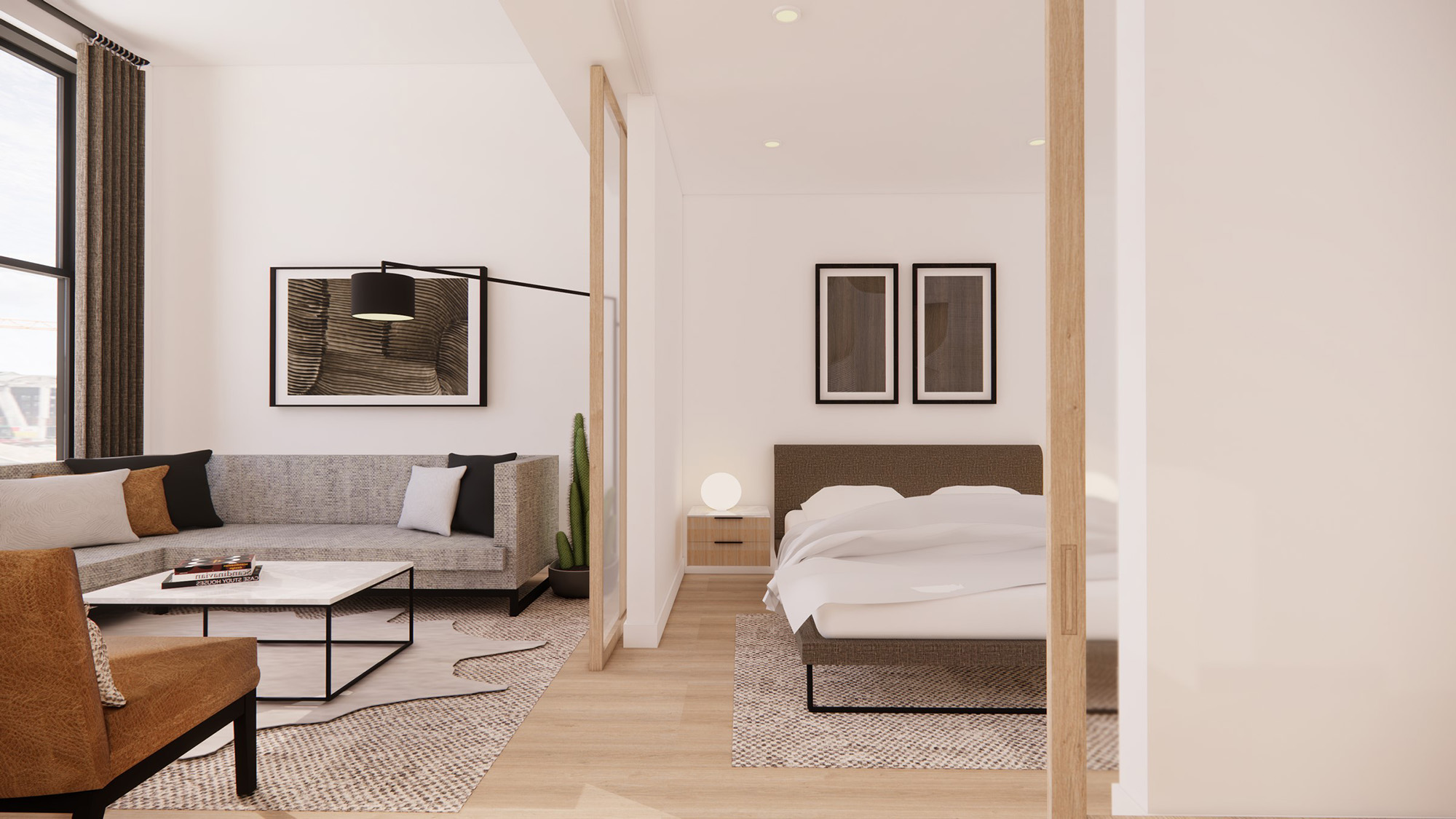
Related Stories
| Aug 11, 2010
Decline expected as healthcare slows, but hospital work will remain steady
The once steady 10% growth rate in healthcare construction spending has slowed, but hasn't entirely stopped. Spending is currently 1.7% higher than the same time last year when construction materials costs were 8% higher. The 2.5% monthly jobsite spending decline since last fall is consistent with the decline in materials costs.
| Aug 11, 2010
Luxury Hotel required faceted design
Goettsch Partners, Chicago, designed a new five-star, 214-room hotel for the King Abdullah Financial District (KAFD) in Riyadh, Saudi Arabia. The design-build project, with Saudi Oger Ltd. as contractor and Rayadah Investment Co. as developer, has a three-story podium supporting a 17-story glass tower with a nine-story opening that allows light to penetrate the mass of the building.
| Aug 11, 2010
U.S. firm designing massive Taiwan project
MulvannyG2 Architecture is designing one of Taipei, Taiwan's largest urban redevelopment projects. The Bellevue, Wash., firm is working with developer The Global Team Group to create Aquapearl, a mixed-use complex that's part of the Taipei government's "Good Looking Taipei 2010" initiative to spur redevelopment of the city's Songjian District.
| Aug 11, 2010
7 Keys to Unlocking Energy Efficiency in Schools
Today’s best K-12 schools are embracing the sustainability ethos in their design and construction, and that can mean a healthier, more comfortable indoor environment and improved learning. Some studies contend that ample amounts of daylighting, for example, lead to higher test scores. High-performance HVAC systems that constantly draw fresh air into a classroom seem to help both teachers ...
| Aug 11, 2010
Great Solutions: Green Building
27. Next-Generation Green Roofs Sprout up in New York New York is not particularly known for its green roofs, but two recent projects may put the Big Apple on the map. In spring 2010, the Lincoln Center for the Performing Arts will debut one of the nation's first fully walkable green roofs. Located across from the Juilliard School in Lincoln Center's North Plaza, Illumination Lawn will consist ...
| Aug 11, 2010
Giants 300 University Report
University construction spending is 13% higher than a year ago—mostly for residence halls and infrastructure on public campuses—and is expected to slip less than 5% over the next two years. However, the value of starts dropped about 10% in recent months and will not return to the 2007–08 peak for about two years.
| Aug 11, 2010
World's tallest all-wood residential structure opens in London
At nine stories, the Stadthaus apartment complex in East London is the world’s tallest residential structure constructed entirely in timber and one of the tallest all-wood buildings on the planet. The tower’s structural system consists of cross-laminated timber (CLT) panels pieced together to form load-bearing walls and floors. Even the elevator and stair shafts are constructed of prefabricated CLT.
| Aug 11, 2010
Great Solutions: Healthcare
11. Operating Room-Integrated MRI will Help Neurosurgeons Get it Right the First Time A major limitation of traditional brain cancer surgery is the lack of scanning capability in the operating room. Neurosurgeons do their best to visually identify and remove the cancerous tissue, but only an MRI scan will confirm if the operation was a complete success or not.
| Aug 11, 2010
29 Great Solutions
1. Riverwalk Transforms Chicago's Second Waterfront Chicago has long enjoyed a beautiful waterfront along Lake Michigan, but the Windy City's second waterfront along the Chicago River was often ignored and mostly neglected. Thanks to a $22 million rehab by local architect Carol Ross Barney and her associate John Fried, a 1.
| Aug 11, 2010
High-Performance Modular Classrooms Hit the Market
Over a five-day stretch last December, students at the Carroll School in Lincoln, Mass., witnessed the installation of a modular classroom building like no other. The new 950-sf structure, which will serve as the school's tutoring offices for the next few years, is loaded with sustainable features like sun-tunnel skylights, doubled-insulated low-e glazing, a cool roof, light shelves, bamboo tri...