Value engineering brings Santa Barbara apartments back on track
Although demand for housing in the area was rising rapidly, development of a new apartment complex in Rialto, California, had stalled. Estimates for the complex’s framing costs were coming in high, and the project just wasn’t penciling out. So the developer, Barbara Monroy of BM Investments Company, took a fresh look at the design of the project.
At the advice of her framing contractor, Monroy turned to Amir Deihimi, PE, of Core Structure, Inc., who helped identify ways to build the project more efficiently while maintaining the structural integrity of the buildings.
At seven buildings with 120 units altogether, this presented a challenge. Each building, at about 20,000 square feet each, is unique with one-, two- and three-bedroom apartments located above on-grade garages. Each garage has its own private stairway to the unit above.
“The Santa Barbara Complex is literally on top of a southern California fault line, so the seismic loads are significant,” said Deihimi. “But there are more affordable engineering solutions, and they had not been fully explored.”
Deihimi replaced expensive steel framing with I-joist compatible glulam and double-sided wood structural panel portal frames using force transfer around openings (FTAO), a method of shear wall analysis popular in California that cut costs drastically without cutting seismic performance.
Core Structure initially focused the value engineering process on the prefabricated steel shear walls. Each apartment has its own garage and in the original design, each garage had four steel shear walls (two back-to-back). To replace the expensive steel walls, Core Structure designed a cost-effective double-sided wood structural panel portal frame with force transfer around openings shear wall analysis. The same method was used around the entire exterior of the building at the window openings.
“The only thing we needed to add was the sheathing above and below the header,” said Deihimi. “And if we’re not doing that for shear, the framer has to fur it out anyway. Plus, the straps help us eliminate two hold-downs next to the opening. Often, those are HD-type hold-downs, which can be costly and difficult to install. But by using FTAO, we just ended up with a strap on each far end of the wall for this particular design.”
To learn more about the project and force transfer around openings (FTAO), visit Value Engineering on Designers Circle.
About the Author
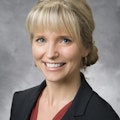
Karyn Beebe
Karyn Beebe, PE, LEED AP is an Engineered Wood Specialist for APA-The Engineered Wood Association. Her duties include consulting with designers on the efficient specification of engineered wood products in construction. A licensed Professional Engineer in the state of California, Beebe graduated from Purdue University with a BS in Civil Engineering. She is an active member of the Structural Engineers Association and the U.S. Green Building Council, and serves as President for the San Diego Area Chapter of the ICC. Prior to joining APA, Beebe worked as a structural engineer and structural plan reviewer for the San Diego building department.