Prefabricated modular design and construction have made notable inroads into such sectors as industrial, residential, hospitality and, more recently, office and healthcare. But Dafna Kaplan thinks that what’s held back the modular building industry from even greater market penetration has been suppliers’ insistence that they do everything: design, manufacture, logistics, land prep, assembly, even onsite construction. “That’s been their Achilles’ Heel.”
Kaplan is CEO and Founder of Cassette, a Los Angeles-based startup that designs and sells stackable apartment-living pods with move-in-ready 80-sf kitchens, 60-sf bathrooms, 130-sf bedrooms with double wardrobe, and 162-sf living rooms. Last October, Cassette unveiled its 600-sf, one-bedroom model unit designed by Craig Hodgetts and Ming Fung of HplusF Design Lab in Culver City, Calif., at a popup showroom open for tours.
Cassette started in 2019, but was stalled for a while by Covid-19 restrictions. During that lull, Kaplan—who previously worked in an advisory capacity with ConXTech and MATT Construction—did a lot of consulting. The Covid period also saw some high-profile modular manufacturers stumble and fall, which gave Kaplan insight into what did and didn’t work. During the year before Cassette introduced its product, Kaplan also benefited from conversations with industry leaders like RAD Urban’s Co-founder Randy Miller and FullStack Modular’s CEO Roger Krulak.
Her main takeaway from all this: “We learned not to do too much.”
Savings from modular construction come from process improvements
Proponents have long touted modular as an answer to helping lessen America’s chronic housing shortage and rising construction costs, and Kaplan is no different. Cassette’s “mission” is to reduce the cost of multifamily housing construction by 30% in three years, and double the speed of housing production. By focusing half of the building design toward a fixed product/fixed price model, Cassette would bring more predictability to construction.
“The trick to reducing construction costs is to get the entire system to function in unison,” Kaplan tells BD+C. The cost savings will come, over time, from process improvements “and getting better with every iteration.”
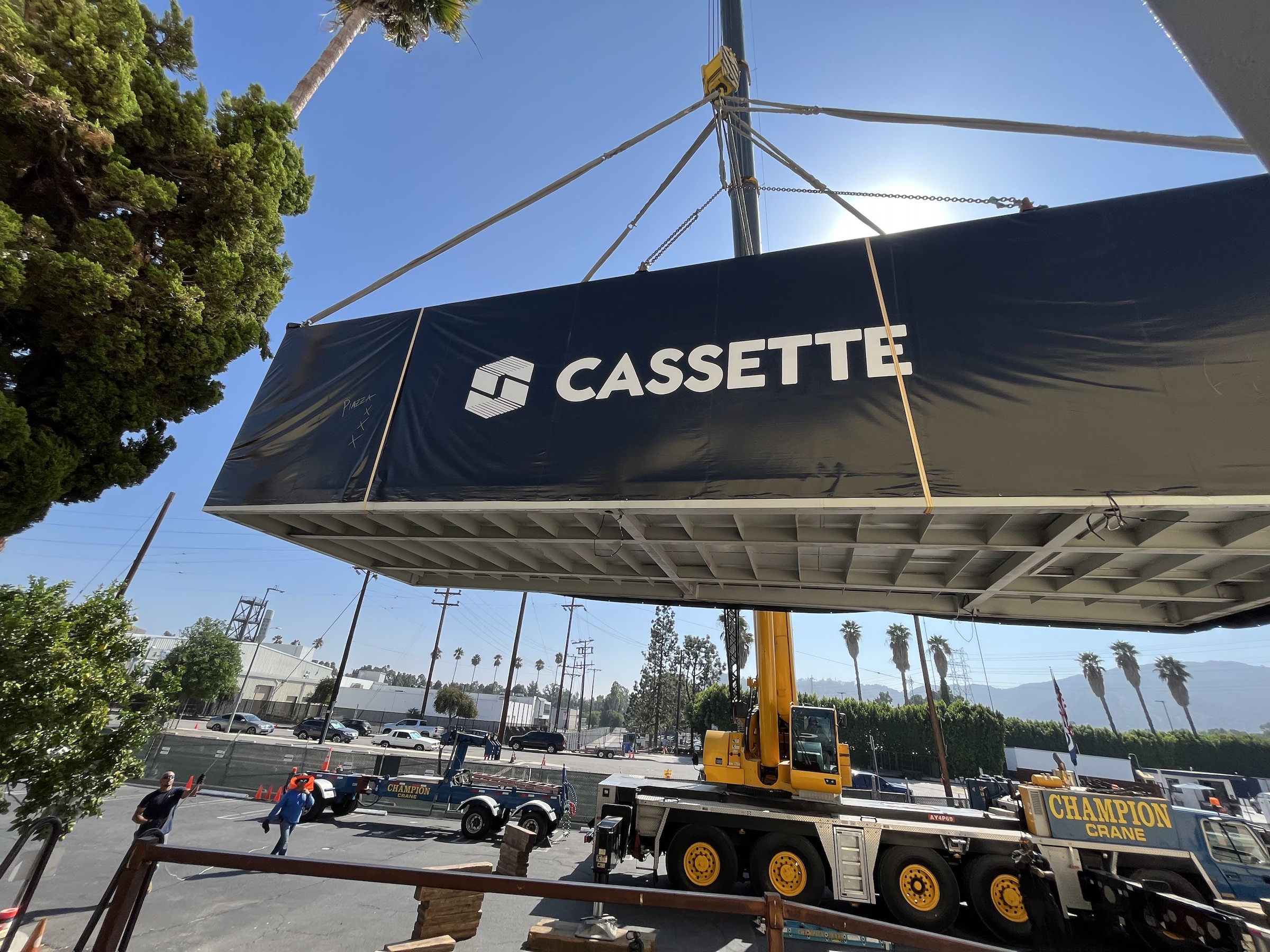
Hodgetts of HPlusF Design Lab, who holds two modular patents, adds that great design “doesn’t have to be expensive,” and asserts that Cassette’s formula of developing a product through a lens of manufacturing and prefab will “make modular construction a practical reality.” (The designers and Nick Butcher, Cassette's COO, knew each other previously and had worked together before. “It was a mind meld of mutual respect,” says Kaplan.)
Modular building units in production in 2023
Kaplan says that what separates Cassette from its competitors starts with price transparency. Modular suppliers are often circumspect about comparing their prices with conventional design and construction. Cassette states its pricing upfront, and while it doesn’t require minimum orders, discounts are available when customers buy more, ranging from $170,000 per unit for orders under 15 units, to $140,000 with orders of 101 to 300 units, with incremental price reductions in between.
Pricing covers predevelopment design team coordination, interior design, floor-to-ceiling window/sliding door systems, 100% preinstalled waterproofing, major appliances, tankless water heater, all fixtures and finishes, a split HVAC system evaporator coil, and onsite delivery, installation, and structural hookup.
When interviewed in November, Kaplan said her company was “in discussions” with a half-dozen general contractors. Cassette also has manufacturing contracts with factories in Malaysia and South Korea, and was in discussions with a factory in Mexico. (Kaplan notes that the supply chain, and not the logistics, is the most critical part of the modular business.) From order to delivery will take about six months, she estimates.
The 14.5x43-foot product is sized so that “you don’t need a police car on the road to transport it,” says Kaplan. The pods are stackable up to six stories and include bracket support for attaching balconies and corridors. (Sitework includes elevators and stairs, and there are extra costs for roof slope and membrane, foundations, public circulation areas, and additional exterior façade.)
Late last year, Cassette was taking orders, and Kaplan fully expects to be building projects in 2023. She didn’t reveal much, except to say that one project in Los Angeles County will be 30 units, and another 200. Cassette eventually plans to expand its assortment to include studio and two-bedroom pods. Kaplan is also keeping an eye on renter demographics to gauge future demand for different apartment sizes and features. “It’s all about good architecture and design,” she says.
Related Stories
| May 2, 2014
Norwegian modular project set to be world's tallest timber-frame apartment building [slideshow]
A 14-story luxury apartment block in central Bergen, Norway, will be the world's tallest timber-framed multifamily project, at 49 meters (160 feet).
| May 1, 2014
Tight on space for multifamily? Check out this modular kitchen tower
The Clei Ecooking kitchen, recently rolled out at Milan's Salone de Mobile furniture fair, squeezes multiple appliances into a tiny footprint.
| Apr 30, 2014
Visiting Beijing's massive Chaoyang Park Plaza will be like 'moving through a urban forest'
Construction work has begun on the 120,000-sm mixed-use development, which was envisioned by MAD architects as a modern, urban forest.
| Apr 29, 2014
Best of Canada: 12 projects nab nation's top architectural prize [slideshow]
The conversion of a Mies van der Rohe-designed gas station and North Vancouver City Hall are among the recently completed projects to win the 2014 Governor General's Medal in Architecture.
| Apr 29, 2014
USGBC launches real-time green building data dashboard
The online data visualization resource highlights green building data for each state and Washington, D.C.
| Apr 23, 2014
Developers change gears at Atlantic Yards after high-rise modular proves difficult
At 32 stories, the B2 residential tower at Atlantic Yards has been widely lauded as a bellwether for modular construction. But only five floors have been completed in 18 months.
| Apr 17, 2014
Online mapping tool helps teams determine multifamily project tax credit eligibility
Accounting and advisory firm Baker Tilly has launched a new, interactive online mapping tool that helps users determine if a business or development project may qualify for the New Markets Tax Credit or Low-Income Housing Tax Credit program.
| Apr 11, 2014
ULI report documents business case for building healthy projects
Sustainable and wellness-related design strategies embody a strong return on investment, according to a report by the Urban Land Institute.
| Apr 9, 2014
Steel decks: 11 tips for their proper use | BD+C
Building Teams have been using steel decks with proven success for 75 years. Building Design+Construction consulted with technical experts from the Steel Deck Institute and the deck manufacturing industry for their advice on how best to use steel decking.
| Apr 2, 2014
8 tips for avoiding thermal bridges in window applications
Aligning thermal breaks and applying air barriers are among the top design and installation tricks recommended by building enclosure experts.