The building was large, but not unusual, with an equally sizeable floor sheathed with OSB. What was unusual was the enormous amount of rain that unexpectedly doused the site during construction. Luckily, the developers had the foresight to include temporary expansion joints, and the project continued without a hitch after the deluge dried up.
While temporary expansion joints may seem like a minor detail, omitting them can have severe consequences where humidity or moisture come into play. When wood structural panels (plywood and OSB) are exposed to moisture during construction, the wood absorbs moisture, and panel expansion may occur.
“We recently saw an example of just how important expansion joint detailing is,” said Karyn Beebe, PE, an engineered wood specialist for APA. “In a large condominium project, a 174-foot long floor was exposed to nine inches of rain within two months during the framing stage of construction. The floor panels expanded and the framer reported the first story walls were leaning out of plumb up to 1-1/2 inches, forcing the crew to realign the walls.”
The accumulated panel expansion and resulting misalignment occurred in the first phase of a two-phase development. The design team was able to learn from the incident and incorporate temporary expansion joints in the plans for the second phase of the project.
For smaller buildings, the recommended 1/8-inch spacing of floor, wall or roof sheathing panels will usually allow panels to expand without affecting wall alignment, assuming no unusual moisture conditions or aggressive fastening schedules. The larger the building, the larger the potential for adverse effects to framing caused by expansion of moisture-laden panels, Beebe explained. In large buildings with continuous floor or roof decks constructed of plywood or OSB, the effects can be more noticeable. Results of the expansion can include the displacement of framing at the building’s perimeter and out-of-square window and door openings.
Builders can eliminate displacement from the equation during construction by using temporary expansion joints for buildings that have a length or width exceeding 80 feet. This should be done in addition to providing 1/8-inch spacing at all panel ends and edges.
Temporary Expansion Joints for Large Floors
These joints consist of an extra-wide spacing gap, such as 3/4 inch for floors, between panel ends at the desired expansion intervals. Panel ends can be supported on adjacent doubled floor joists, but not fastened to them until later, allowing for expansion. (Temporarily placed panels should be held in place with enough fasteners to prevent unsafe jobsite conditions, such as fall or trip hazards.) It is also important to ensure that wall bottom plates do not extend across the expansion joint. After the building is closed in, fastening of the floor panels can be completed. If necessary, a filler piece or non-shrink grout can be installed to fill the gap between panels. For shear walls or braced wall panels, a short lumber bottom plate filter block and doubler can be added between studs to splice the bottom plate of walls over the expansion joint.
Temporary Expansion Joints for Large Roof Decks
While constructing large roof decks, sheath 80-foot sections at a time, omitting a roof panel between sections. This provides effective temporary expansion joints. The installation can be completed with “fill-in” panels cut to size as necessary. Cover the roof deck with roofing underlayment as soon as practicable for protection against excessive moisture prior to roofing application. This process can be scheduled in sections to avoid exposing an entire expanse of roof deck to weathering during construction.
Curtail Callbacks and Corrections
While designers or contractors may opt out of including temporary expansion joints in large buildings—for example, in warm, dry regions or in summer months—this omission should be undertaken in the full understanding that the designer or contractor may face the potential risk of structural modifications or repairs if moisture-related expansion causes problems. Incorporating temporary expansion joints in large buildings is good construction practice, and APA recommends this for all buildings 80 feet or greater in length or width.
For more detailed information on temporary expansion joints, including temporary drainage holes, consult APA Technical Note: Temporary Expansion Joints for Large Buildings, Form U425. For more information on wood frame construction for commercial structures, visit APA Designers Circle.
About the Author
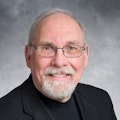