Operations and maintenance: The missing link in BIM/VDC coordination
For as much progress as Building Teams have made over the past decade with regard to 3D BIM/VDC coordination on building projects, even the most ardent BIM adopters have neglected what is perhaps the most vital component of any project—operations and maintenance processes and procedures.
Don’t get me wrong: Any building owner or developer would gladly welcome the upfront savings in cost and schedule—along with a higher-quality built environment—that BIM/VDC coordination typically delivers. But the scope of any immediate savings gained by using BIM/VDC pales in comparison to the ongoing efficiencies and cost avoidances that can be achieved by producing a building that is markedly easier and safer to service over its life. And the gains are even greater for owners of legacy buildings—hospitals, schools, government facilities—where 100-year life spans are the norm. Something as minor as a hard-to-access ventilation fan or a poorly specified flooring system can result in decades of added costs for the owner.
Of course, BIM/VDC is not a silver bullet for solving all O&M issues. It’s a communication tool—a database with a nifty graphics interface—that can foster a deeper level of collaboration between members of the Building Team. The real advancement will come in the form of BIM/VDC/IPD project contracts that mandate O&M coordination from the earliest stages of planning.
Progressive Building Teams are beginning to explore the possibilities of O&M BIM/VDC coordination. The team for the Ann & Robert H. Lurie Children’s Hospital of Chicago, for instance, incorporated a number of O&M processes in the design scheme. However, as some of the stakeholders on the project admit, the Building Team only scratched the surface.
“Looking back, there’s so much more we could have done,” Eric Hoffman, Administrator of Facility Services at Lurie Children’s, told me during a recent tour. He identified several areas where BIM/VDC coordination can result in a meaningful impact to O&M efforts:
- Lean operations. It’s hard to find a healthcare organization that is not implementing some type of Lean operations program. BIM coordination can be a powerful tool for eliminating waste in process and product. Think of the thousands of health/safety inspections and preventive maintenance exercises that an O&M team must execute in a given year. By reducing the time it takes to complete these tasks (for example, by optimizing the path for inspecting fire/life safety systems), building owners can save hundreds—if not thousands—of man-hours each year.
- FM system integration. Turning a building over to the owner is a messy process, and one of the more tedious tasks is integrating the building’s as-built data into the facility management system. Are there ways to automate this process using the data in the BIM model? That’s the million-dollar question BIM experts are trying to answer.
- Space management. Having an accurate as-built model can be helpful not only for reconstruction planning, but also for financial analysis of the space (e.g., amount of revenue being generated in a given space, ROI for renovations, best use of a particular space, etc.).
On future projects, expect your client’s O&M team—from the facilities director down to “Bob the boiler expert”—to have a seat at the design table. It’s just good business sense for any owner, especially those who are in it for the long haul.
About the Author
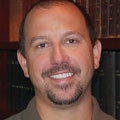
David Barista
David Barista is Editorial Director of Building Design+Construction and BDCnetwork.com, properties that combined reach more than 100,000 commercial building professionals, including architects, engineers, contractors, and building owners. David has covered the U.S. construction industry for more than a decade, previously serving as Editor-in-Chief of BD+C, Professional Builder, Custom Builder, and HousingZone.com. He has won numerous editorial awards, including six Jesse H. Neal Awards and multiple honors from the Construction Writers Association and the American Society of Business Publication Editors.
Email: dbarista@sgcmail.com