Next February, FullStack Modular, a leading supplier of prefabricated modules, is scheduled to begin production for its first project in California, a, 86,000-sf, six-story, 143-room hotel that will be the Treehouse Hotel brand’s debut in the United States.
Starwood Capital Group launched Treehouse in 2019 as a eco-friendly lifestyle concept. It currently operates three properties in the United Kingdom, and is developing the U.S. project through its brands management company SH Hotels and Resorts. Its American hotel will be located in Sunnyvale, Calif., and is expected to open late next year. (Starwood is also repurposing several existing structures onsite for additional hotel rooms and suites.)
In an interview with BD+C, Roger Krulak, FullStack Modular’s president and founder, said that his company will produce 200 modules for this project from its manufacturing plant in Portland, Ore. (FullStack’s other plant is in Brooklyn, N.Y.) He estimates that the production would take less than six months, and assembly another three months. Scottsdale, Ariz.-based Synergy Modular is the project’s general contractor.
Krulak believes that Starwood chose FullStack Modular for its fully integrated system approach: its modules are delivered with electrical, plumbing, and mechanical components and systems installed. The building’s façade is also installed at the factory, as are each units’ fixtures and finishes. The building doesn’t require a concrete core and, where necessary, can be rigged at the factory for seismic resistance. Even furniture can be included. The only on-site construction, said Krulak, involves the building’s hallways and elevators.
According to Starwood, the majority of Treehouse’s rooms will provide private outdoor spaces that include ground floor patios and balconies and terraces on the upper floors.
“The FullStack Modular system is one of the most volumetric modular systems anywhere,” said Andy Nuessle, Synergy Modular’s president, in a prepared statement. “The hotel is 100 percent modular from the foundation to the roof.”
Starwood Capital has not disclosed the cost of the Sunnyvale Treehouse Hotel. On its website, FullStack Modular states that, in general, modular production reduces construction costs by as much as 20 percent, construction time by as much as 50 percent, and construction waste by as much as 67 percent. Krulak estimated that the Sunnyvale project will be completed 30 to 40 percent faster than it would were it build using convention on-site construction methods.
A sliver, but increasing
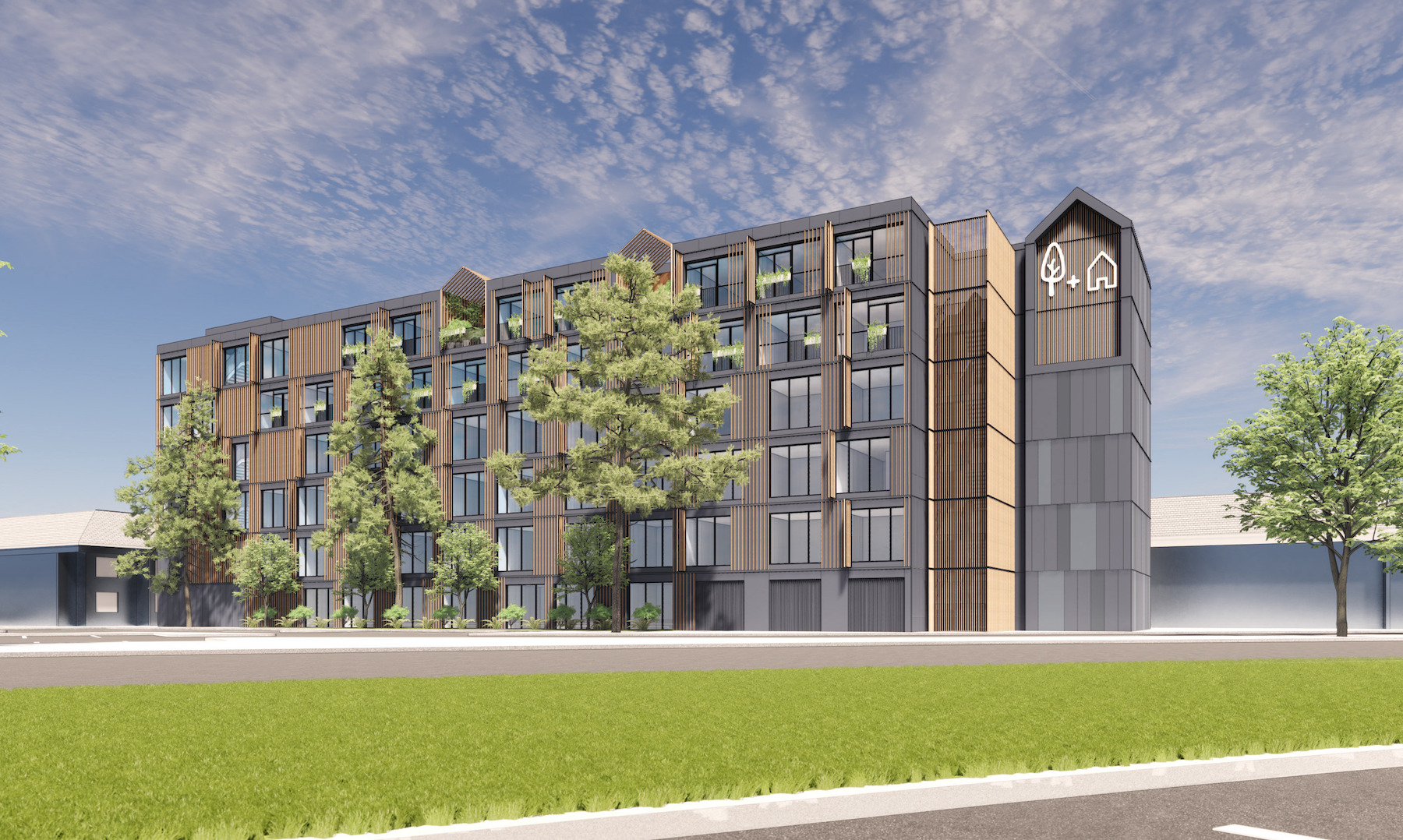
The Modular Building Institute estimates that buildings assembled from modules produced offsite accounted for 5.52 percent of all new construction in North America in 2021. That represented a doubling of market share in five years, and Tom Hardiman, the Institute’s executive director, told the website Construction Dive that he expects modular’s share to rise to 10 percent by 2026.
Krulak is also optimistic about modular’s growth, especially on the residential side. “Housing in the U.S. is at a huge deficit, and construction has no capacity to meet that need. So off-site solutions are picking up significantly. We get a call almost every day.”
Krulak said that FullStack Modular is looking at “a number of opportunities” in the U.S. and internationally. Earlier this month, the company announced it had entered into a strategic alliance with Saudi Arabian Baytur Construction to pursue opportunities for Vision 2030, a large-scale hospitality and urban tourism initiative whose key goal is to increase the Kingdom’s overall hospitality capacity by more than 70,000 hotel rooms.
Related Stories
| May 30, 2014
MIT researchers create 'home in a box' transformable wall system for micro apartments
Dubbed CityHome, the system integrates furniture, storage, exercise equipment, lighting, office equipment, and entertainment systems into a compact wall unit.
| May 29, 2014
7 cost-effective ways to make U.S. infrastructure more resilient
Moving critical elements to higher ground and designing for longer lifespans are just some of the ways cities and governments can make infrastructure more resilient to natural disasters and climate change, writes Richard Cavallaro, President of Skanska USA Civil.
| May 27, 2014
Contractors survey reveals improving construction market
The construction industry is on the road to recovery, according to a new survey by Metal Construction News. Most metrics improved from the previous year’s survey, including a 19.4% increase in the average annual gross contracting sales volume. SPONSORED CONTENT
| May 26, 2014
New Jersey data centers will manage loads with pods
The two data center facilities totaling almost 430,000 sf for owner Digital Realty Trust will use the company's TK-Flex planning module, allowing for 24 pods.
| May 22, 2014
BIM-driven prototype turns data centers into a kit of parts
Data center design specialist SPARCH creates a modular scheme for solutions provider Digital Realty.
| May 19, 2014
What can architects learn from nature’s 3.8 billion years of experience?
In a new report, HOK and Biomimicry 3.8 partnered to study how lessons from the temperate broadleaf forest biome, which houses many of the world’s largest population centers, can inform the design of the built environment.
| May 14, 2014
Prefab payback: Mortenson quantifies cost and schedule savings from prefabrication techniques
Value-based cost-benefit analysis of prefab approaches on the firm's 360-bed Exempla Saint Joseph Heritage Project shows significant savings for the Building Team.
| May 13, 2014
19 industry groups team to promote resilient planning and building materials
The industry associations, with more than 700,000 members generating almost $1 trillion in GDP, have issued a joint statement on resilience, pushing design and building solutions for disaster mitigation.
| May 11, 2014
8 starter questions to answer when thinking about building
So, are you ready to start building? Completing these eight questions will help you answer that confidently. SPONSORED CONTENT
| May 11, 2014
Final call for entries: 2014 Giants 300 survey
BD+C's 2014 Giants 300 survey forms are due Wednesday, May 21. Survey results will be published in our July 2014 issue. The annual Giants 300 Report ranks the top AEC firms in commercial construction, by revenue.