Get ready for a surge in prefabrication activity by contractors.
FMI, the consulting and investment banking firm, recently polled contractors about how much time they were spending, in craft labor hours, on prefabrication for construction projects. More than 250 contractors participated in the survey, and the average response to that question was 18%. More revealing, however, was the participants’ anticipation that craft hours dedicated to prefab would essentially double, to 34%, within the next five years.
The study—a sequel to FMI’s 2023 Labor Productivity Study—reiterates how the industry’s receptivity to prefab solutions corresponds with its ongoing labor shortages and compressed project schedules. (Contractors experienced approximately $30 billion to $40 billion in lost profits due to labor inefficiencies in 2022.) In its latest study, contractors told FMI that “improved quality” was prefab’s greatest perceived benefit. “Reducing the risk and variability” is how one contractor put it. Other benefits cited include reductions in construction schedules and improved worker safety.
(Nearly three fifths of the respondents to FMI’s study are MEP contractors, with another 15% being framing and drywall contractors.)

Contractors that consider prefabrication must determine how to do it at scale, profitably, and in a way that increases company earnings. Successful prefab practices, says FMI, require long-term strategic thinking and planning across an organization, along with the development of a comprehensive operational blueprint.
Which prefab model is right for pros?
It’s not like prefabrication is an alien concept for contractors. FMI’s study found that 86% of respondents currently offer single-trade prefab services. Three quarters of the concrete contractors surveyed said they are prefabricating on their jobsites; 57% of self-performing general contractors polled are prefabbing on-site, too.
What’s often lacking, however, is a clear vision of what they want their prefab capabilities to become. To make prefab work, says FMI, contractors need to shift their operating models, processes and systems. Contractors also need to decide which prefab models and combinations would work best for their companies; these include kitting services, multi-trade services, procurement, and modular services.
In making these determinations, contractors should be asking themselves:
•Why do we want to do more prefabrication?
•What is the total addressable portion of our work mix (today) that could be prefabricated?
•What investments would need to be made to scale our prefabrication capabilities to capture that opportunity?
•When fully optimized, what does the earnings stream from prefabrication look like?
•What does the return on investment look like for the enterprise?
•Do we have alternative investment options for other initiatives in the business? How do those options stack up against our prefabrication ambitions?
•Will prefab make the company better, more profitable, and resilient?
Prefabrication a different kind of business
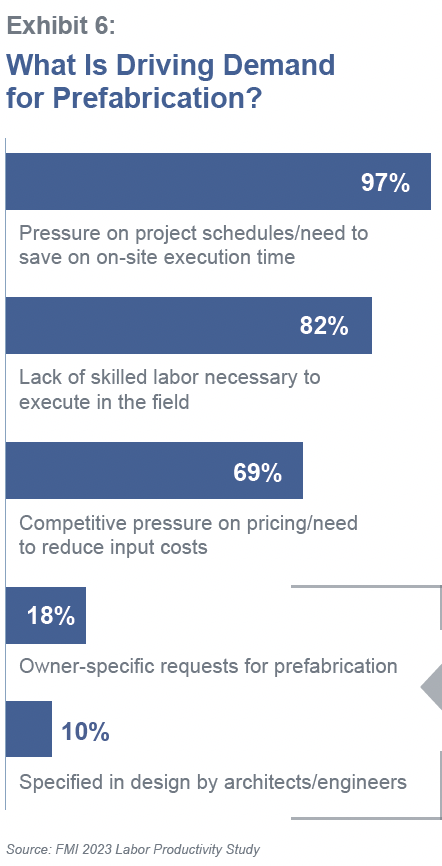
Prefabrication is a manufacturing endeavor that’s different from building construction. Contractors diving into prefab in a bigger way need to think about whether prefab will be a unique business or separate entity, and how autonomously construction and prefabrication operate? Will prefab services be proprietary or available to other contractors? Will prefab be a profit or cost center? How will manufacturing cost overruns, if there are any, be accounted for?
FMI says that contractors need to establish clear project management lines that encompass how prefabricated products are tracked, stored, and billed for. Tracking labor productivity across prefabrication and field installation is key.
Owners and designers need to buy in more
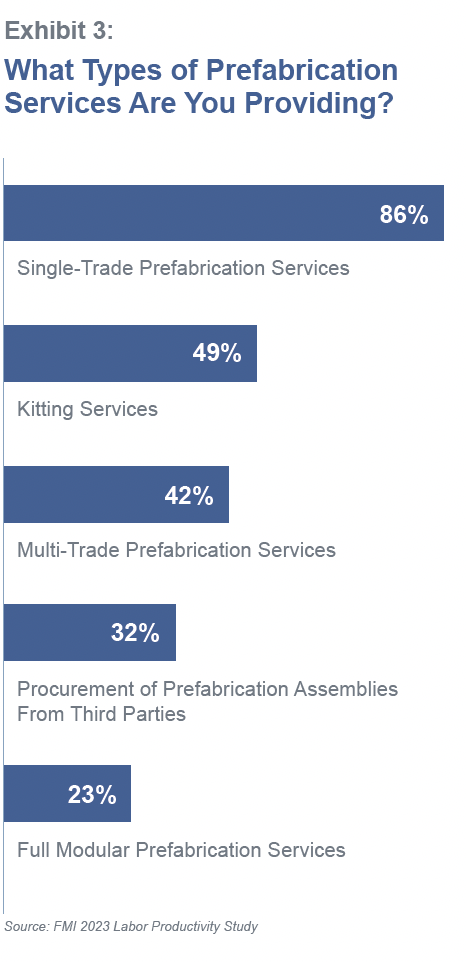
One of the contractors whom FMI polled mentioned a recent casino and hotel project that required 25% less labor in the field, and cut nearly two months off of its installation time, by using prefabrication methods.
Scheduling is driving prefab demand, says FMI. But expanding that demand depends on acceptance by owners and AEC firms, and right now, that acceptance is middling: only 18% of the contractors polled by FMI said that owner-specific requests drove prefab, and only 10% said that prefab was specified by architects or engineers.
“For the industry to realize substantial gains in prefabrication and productivity, owners and designers need to be a bigger part of the demand equation,” says FMI.
FMI’s study found that the industry still struggles with broad adoption. The biggest challenges to adopting prefab are a project’s design and coordination, stakeholder awareness and education, the mindset and culture of a project’s active players, and the investment in facilities and equipment.
But given current and projected labor force limitations, “it’s clear that prefabrication will need to become part of the solution.” For that to happen, building teams need to demonstrate a bolder vision, strategic planning, commitment to investing, consistent communication, and a proactive engagement by external stakeholders.
Related Stories
| Oct 13, 2010
New health center to focus on education and awareness
Construction is getting pumped up at the new Anschutz Health and Wellness Center at the University of Colorado, Denver. The four-story, 94,000-sf building will focus on healthy lifestyles and disease prevention.
| Oct 13, 2010
Community center under way in NYC seeks LEED Platinum
A curving, 550-foot-long glass arcade dubbed the “Wall of Light” is the standout architectural and sustainable feature of the Battery Park City Community Center, a 60,000-sf complex located in a two-tower residential Lower Manhattan complex. Hanrahan Meyers Architects designed the glass arcade to act as a passive energy system, bringing natural light into all interior spaces.
| Oct 13, 2010
Community college plans new campus building
Construction is moving along on Hudson County Community College’s North Hudson Campus Center in Union City, N.J. The seven-story, 92,000-sf building will be the first higher education facility in the city.
| Oct 13, 2010
Bookworms in Silver Spring getting new library
The residents of Silver Spring, Md., will soon have a new 112,000-sf library. The project is aiming for LEED Silver certification.
| Oct 13, 2010
County building aims for the sun, shade
The 187,032-sf East County Hall of Justice in Dublin, Calif., will be oriented to take advantage of daylighting, with exterior sunshades preventing unwanted heat gain and glare. The building is targeting LEED Silver. Strong horizontal massing helps both buildings better match their low-rise and residential neighbors.
| Oct 12, 2010
Holton Career and Resource Center, Durham, N.C.
27th Annual Reconstruction Awards—Special Recognition. Early in the current decade, violence within the community of Northeast Central Durham, N.C., escalated to the point where school safety officers at Holton Junior High School feared for their own safety. The school eventually closed and the property sat vacant for five years.
| Oct 12, 2010
Guardian Building, Detroit, Mich.
27th Annual Reconstruction Awards—Special Recognition. The relocation and consolidation of hundreds of employees from seven departments of Wayne County, Mich., into the historic Guardian Building in downtown Detroit is a refreshing tale of smart government planning and clever financial management that will benefit taxpayers in the economically distressed region for years to come.
| Oct 12, 2010
Richmond CenterStage, Richmond, Va.
27th Annual Reconstruction Awards—Bronze Award. The Richmond CenterStage opened in 1928 in the Virginia capital as a grand movie palace named Loew’s Theatre. It was reinvented in 1983 as a performing arts center known as Carpenter Theatre and hobbled along until 2004, when the crumbling venue was mercifully shuttered.
| Oct 12, 2010
University of Toledo, Memorial Field House
27th Annual Reconstruction Awards—Silver Award. Memorial Field House, once the lovely Collegiate Gothic (ca. 1933) centerpiece (along with neighboring University Hall) of the University of Toledo campus, took its share of abuse after a new athletic arena made it redundant, in 1976. The ultimate insult occurred when the ROTC used it as a paintball venue.
| Oct 12, 2010
Owen Hall, Michigan State University, East Lansing, Mich.
27th Annual Reconstruction Awards—Silver Award. Officials at Michigan State University’s East Lansing Campus were concerned that Owen Hall, a mid-20th-century residence facility, was no longer attracting much interest from its target audience, graduate and international students.