Get ready for a surge in prefabrication activity by contractors.
FMI, the consulting and investment banking firm, recently polled contractors about how much time they were spending, in craft labor hours, on prefabrication for construction projects. More than 250 contractors participated in the survey, and the average response to that question was 18%. More revealing, however, was the participants’ anticipation that craft hours dedicated to prefab would essentially double, to 34%, within the next five years.
The study—a sequel to FMI’s 2023 Labor Productivity Study—reiterates how the industry’s receptivity to prefab solutions corresponds with its ongoing labor shortages and compressed project schedules. (Contractors experienced approximately $30 billion to $40 billion in lost profits due to labor inefficiencies in 2022.) In its latest study, contractors told FMI that “improved quality” was prefab’s greatest perceived benefit. “Reducing the risk and variability” is how one contractor put it. Other benefits cited include reductions in construction schedules and improved worker safety.
(Nearly three fifths of the respondents to FMI’s study are MEP contractors, with another 15% being framing and drywall contractors.)

Contractors that consider prefabrication must determine how to do it at scale, profitably, and in a way that increases company earnings. Successful prefab practices, says FMI, require long-term strategic thinking and planning across an organization, along with the development of a comprehensive operational blueprint.
Which prefab model is right for pros?
It’s not like prefabrication is an alien concept for contractors. FMI’s study found that 86% of respondents currently offer single-trade prefab services. Three quarters of the concrete contractors surveyed said they are prefabricating on their jobsites; 57% of self-performing general contractors polled are prefabbing on-site, too.
What’s often lacking, however, is a clear vision of what they want their prefab capabilities to become. To make prefab work, says FMI, contractors need to shift their operating models, processes and systems. Contractors also need to decide which prefab models and combinations would work best for their companies; these include kitting services, multi-trade services, procurement, and modular services.
In making these determinations, contractors should be asking themselves:
•Why do we want to do more prefabrication?
•What is the total addressable portion of our work mix (today) that could be prefabricated?
•What investments would need to be made to scale our prefabrication capabilities to capture that opportunity?
•When fully optimized, what does the earnings stream from prefabrication look like?
•What does the return on investment look like for the enterprise?
•Do we have alternative investment options for other initiatives in the business? How do those options stack up against our prefabrication ambitions?
•Will prefab make the company better, more profitable, and resilient?
Prefabrication a different kind of business
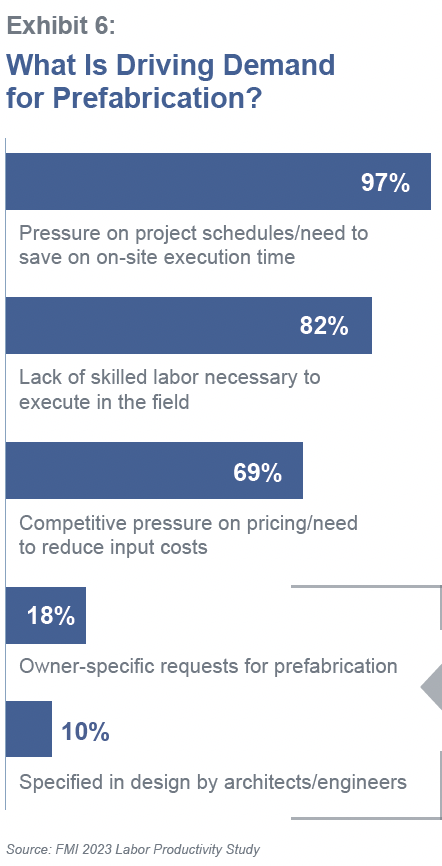
Prefabrication is a manufacturing endeavor that’s different from building construction. Contractors diving into prefab in a bigger way need to think about whether prefab will be a unique business or separate entity, and how autonomously construction and prefabrication operate? Will prefab services be proprietary or available to other contractors? Will prefab be a profit or cost center? How will manufacturing cost overruns, if there are any, be accounted for?
FMI says that contractors need to establish clear project management lines that encompass how prefabricated products are tracked, stored, and billed for. Tracking labor productivity across prefabrication and field installation is key.
Owners and designers need to buy in more
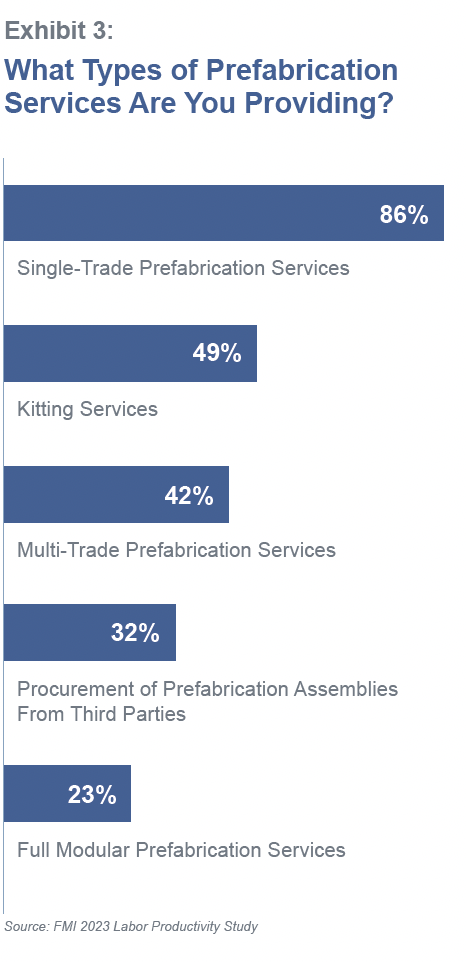
One of the contractors whom FMI polled mentioned a recent casino and hotel project that required 25% less labor in the field, and cut nearly two months off of its installation time, by using prefabrication methods.
Scheduling is driving prefab demand, says FMI. But expanding that demand depends on acceptance by owners and AEC firms, and right now, that acceptance is middling: only 18% of the contractors polled by FMI said that owner-specific requests drove prefab, and only 10% said that prefab was specified by architects or engineers.
“For the industry to realize substantial gains in prefabrication and productivity, owners and designers need to be a bigger part of the demand equation,” says FMI.
FMI’s study found that the industry still struggles with broad adoption. The biggest challenges to adopting prefab are a project’s design and coordination, stakeholder awareness and education, the mindset and culture of a project’s active players, and the investment in facilities and equipment.
But given current and projected labor force limitations, “it’s clear that prefabrication will need to become part of the solution.” For that to happen, building teams need to demonstrate a bolder vision, strategic planning, commitment to investing, consistent communication, and a proactive engagement by external stakeholders.
Related Stories
University Buildings | Jun 26, 2023
Addition by subtraction: The value of open space on higher education campuses
Creating a meaningful academic and student life experience on university and college campuses does not always mean adding a new building. A new or resurrected campus quad, recreational fields, gardens, and other greenspaces can tie a campus together, writes Sean Rosebrugh, AIA, LEED AP, HMC Architects' Higher Education Practice Leader.
Standards | Jun 26, 2023
New Wi-Fi standard boosts indoor navigation, tracking accuracy in buildings
The recently released Wi-Fi standard, IEEE 802.11az enables more refined and accurate indoor location capabilities. As technology manufacturers incorporate the new standard in various devices, it will enable buildings, including malls, arenas, and stadiums, to provide new wayfinding and tracking features.
Contractors | Jun 26, 2023
Most top U.S. contractors rarely deliver projects on time: new study
About 63% of leading U.S. contractors are delivering projects out of schedule, according to a survey of over 300 C-suite executives and owners in the construction industry by XYZ Reality. The study implies that the industry is struggling with significant backlogs due, in part, to avoidable defects, scan, and rework.
Green | Jun 26, 2023
Federal government will spend $30 million on novel green building technologies
The U.S. General Services Administration (GSA), and the U.S. Department of Energy (DOE) will invest $30 million from the Inflation Reduction Act to increase the sustainability of federal buildings by testing novel technologies. The vehicle for that effort, the Green Proving Ground (GPG) program, will invest in American-made technologies to help increase federal electric vehicle supply equipment, protect air quality, reduce climate pollution, and enhance building performance.
Office Buildings | Jun 26, 2023
Electric vehicle chargers are top priority for corporate office renters
Businesses that rent office space view electric vehicle (EV) charging stations as a top priority. More than 40% of companies in the Americas and EMEA (Europe, the Middle East and Africa) are looking to include EV charging stations in future leases, according to JLL’s 2023 Responsible Real Estate study.
Laboratories | Jun 23, 2023
A New Jersey development represents the state’s largest-ever investment in life sciences and medical education
In New Brunswick, N.J., a life sciences development that’s now underway aims to bring together academics and researchers to work, learn, and experiment under one roof. HELIX Health + Life Science Exchange is an innovation district under development on a four-acre downtown site. At $731 million, HELIX, which will be built in three phases, represents New Jersey’s largest-ever investment in life sciences and medical education, according to a press statement.
Sports and Recreational Facilities | Jun 22, 2023
NFL's Jacksonville Jaguars release conceptual designs for ‘stadium of the future’
Designed by HOK, the Stadium of the Future intends to meet the evolving needs of all stadium stakeholders—which include the Jaguars, the annual Florida-Georgia college football game, the TaxSlayer.com Gator Bowl, international sporting events, music festivals and tours, and the thousands of fans and guests who attend each event.
Contractors | Jun 22, 2023
Chris Averill named President of Pepper Construction Group
Pepper Construction Group is pleased to announced the promotion of Chris Averill to the position of President. In his new role, Averill will assume leadership responsibility for the Pepper Construction Group’s growth and performance.
Industrial Facilities | Jun 20, 2023
A new study presses for measuring embodied carbon in industrial buildings
The embodied carbon (EC) intensity in core and shell industrial buildings in the U.S. averages 23.0 kilograms per sf, according to a recent analysis of 26 whole building life-cycle assessments. That means a 300,000-sf warehouse would emit 6,890 megatons of carbon over its lifespan, or the equivalent of the carbon emitted by 1,530 gas-powered cars driven for one year. Those sobering estimates come from a new benchmark study, “Embodied Carbon U.S. Industrial Real Estate.”
Virtual Reality | Jun 16, 2023
Can a VR-enabled AEC Firm transform building projects?
With the aid of virtual reality and 3D visualization technologies, designers, consultants, and their clients can envision a place as though the project were in a later stage.