Metal panels provide a strong, multifunctional skin for buildings: they shield the interior against the elements, support wind and snow loads, and in many cases provide thermal control and noise insulation. However, every material has its limitations, and steel is vulnerable to corrosion. Fortunately, there are robust, well-proven ways to protect steel so it can perform up to its potential virtually indefinitely.
Metal panels are frequently painted with high-performance paint – and recent developments in coating technology have taken that layer of protection to new heights. But to extend protection even further, builders can take advantage of galvanizing under the coating.
Galvanizing is a process of coating steel or iron with a layer of zinc to protect it. It has been used since the mid-18th century – with modernizations and improvements, of course – and continues to be one of the most widely used steel protections worldwide.
Metal wall panels are galvanized by the hot dip method, in which the steel is literally bathed in molten zinc. Properly applied, zinc galvanizing cannot be peeled off like paint, and it does not delaminate. The zinc diffuses into the steel, bonding the two together into a single piece of metal.
The zinc layer protects the steel in two ways. First, it acts as a physical barrier layer. Water cannot touch the steel because it is covered with zinc.
Second, it causes Galvanism to occur. Galvanism is the phenomenon that occurs when two different metals come into contact in the presence of a conductive fluid called an “electrolyte”. One of the metals will give electrons to the other and the resulting electron flow is the electric current we get from a battery. The three elements together form a “galvanic cell”.
In an interesting historical note, galvanizing got its name from Luigi Galvani, who was an 18th century physicist and physician and one of the earliest experimenters in the discovery of electricity. A colleague of his, Alessandro Volta, invented the electric battery and named the chemically-produced electrical flow "Galvanism" in recognition of his associate.
When Galvanism occurs, the metal that gives up electrons is actually physically diminished and sacrificed to the other metal, which in turn is strengthened. The electron-giver is called the “anode,” and the electron-beneficiary is called the “cathode.” The determination of which metal is sacrificed depends on the composition of their molecules. There is a standard written table of metals called the Galvanic Series, showing which metal gives electrons and which takes in any particular pairing. In the case of zinc and steel, zinc is the sacrificial metal.
In a galvanized steel panel, if both the paint layer and the zinc layer get scratched and steel is exposed to the elements, a galvanic cell can be created. The presence of water greatly accelerates this reaction. The zinc acts as a sacrificial anode along the edge of the scratch, sacrificing electrons and deteriorating, while the steel remains relatively unaffected, stopping rust from spreading under the coating and beyond. This action is often referred to as cathodic protection.
Of course, anytime a metal panel is damaged and steel is exposed, it should be repaired in a timely fashion by priming and re-painting to re-protect the steel and halt the galvanic reaction before the zinc is depleted.
G-90 galvanizing (per ASTM A653 Standard Specification for Steel Sheet, Zinc-Coated (Galvanized) or Zinc-Iron Alloy-Coated (Galvannealed) by the Hot-Dip Process) refers to a galvanized coating of a standard thickness. It indicates a thickness of 0.9 ounces of zinc per square foot of steel. For sheet steel, this is the total for both sides, which equals 0.45 oz per side.
In recent years, alloy coatings have been developed that use a combination of aluminum and zinc, often referred to as AZ-50 or AZ-55. This class of coatings includes Galvalume and Galvalume Plus, patented products consisting of 55% aluminum, 43.4% zinc, and 1.6% silicon. The incorporation of aluminum into the coating increases its durability because aluminum oxides are much harder than zinc oxides. If the protective layers are scratched through to the steel, the zinc immediately surrounding it will act as a sacrificial anode (as in galvanizing), but the aluminum will remain in place, further limiting the progression of corrosion even as the zinc is used up. These aluminum-zinc coatings have proven even more effective than classic galvanizing in applications that require greater durability.
Star Building System’s wall and roof panels take full advantage of these technologies to provide long-lasting performance. Single-layer wall panels are all available with Galvalume Plus coating and Signature 200 or Signature 300 series paint protection. Insulated metal wall panels are available in G-90 galvanizing and/or AZ-50 Aluminum-Zinc coatings.
Buildings located close to the seacoast are more vulnerable to corrosion because the prevalent moisture – sea air – is salty and more corrosive than rain water or snow melt. For these situations, specialty coatings are available to provide increased protection.
Loved today’s chemistry lesson? Want to learn more about protecting your metal buildings for the long, long, long term? Download the full whitepaper here.
About the Author
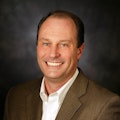
Bob Zabcik
Bob Zabcik is NCI’s Director of Research and Development. He is a LEED Accredited Professional and a Registered Professional Engineer with more than 20 years of experience. He serves on several professional committees such as the MBMA Energy Committee and Sustainability Committee as well as several task groups of those committees. He is also on the Board of the Cool Metal Roofing Coalition and serves as the Director of their technical committee.