Compelling conversations about wood: East and West Coast regional challenges
As part of its Compelling Conversations initiative, APA’s Designers Circle program features thought-leading architects talking with an APA expert about real issues they face when working with engineered wood in commercial applications. This installment features APA Engineered Wood Specialist, Karyn Beebe, in a conversation with sustainability-minded designers Ben Kasdan and Blake Jackson comparing notes on East and West coast approaches to designing with wood, and how innovative design that incorporates sustainability and resilience can influence—and change—the minds of developers.
Karyn: Ben, you're an architectural leader who’s known to push the boundaries in your prominent use of wood on the West Coast. Why do you choose wood and how would you say it contributes to your success?
Ben: Wood is more durable, and it's more flexible in terms of just design application. We can do almost anything we want with it, as long as we're under the height limits of the current codes. It's also more resilient when it comes to seismic load. So it's a very, very useful construction type for us in California.
And we push wood past its traditional code limits. Just about everything we design is in wood. One example is a project we're designing right now in Oakland’s Jack London Square. It's a podium building with two levels in concrete, above grade. Above that, we have five levels of wood construction, plus a mezzanine. So it's effectively an eight-story building and the primary structural component is wood.
Karyn: The West Coast definitely has some seismic concerns. What makes you so confident in wood being able to address those?
Ben: In the early 2000s, Japan actually built a six-story wood multifamily structure on this table that simulates earthquakes. And they just tested the heck out of it. You know what? Because of the redundant nature of wood-frame construction, this thing just performed amazingly. So we have a lot of confidence in its performance seismically.
But really our selection of wood comes down to cost. The land on the West Coast and in California in particular is so expensive that the buildings are already burdened by that construction cost before we've built anything. I'm sure Blake has experienced some of that as well on the East Coast.
Karyn: Well Blake, as our architectural leader on the East Coast, what do you say to that? Seismic issues aren’t a big concern there. So what’s stopping a wider adoption of wood? Especially since it is often a less expensive alternative?
Blake: Ben is right, to a certain extent. East Coast or West Coast, we're under the same money/cost drivers and space constraints in the urban areas. “Getting everything turned around as quickly and cheaply as possible” is certainly the mentality here as well.
But, it’s more than that. We're often stuck with what has worked for developers in the past. They want to eliminate risk as much as possible and they're not really in the business of taking on things that they haven't tried and tested before because at the end of the day, they just want the building. They don't care if we figure out a way to make it with pixie sticks, as long as we can get it built and it starts generating revenue, and they are under that same pressure they place on us by municipal and regulatory bodies to create safe places.
Karyn: Are you saying developers have an aversion to wood on the East Coast? Why would that be?
Blake: It's interesting that we've kind of lost our tradition of wood. I recently got back from a vacation to northern Vermont and I was looking around thinking to myself, “My god, what a readily abundant material that we have here! Why aren't we using it more often?”
But the building types we do—healthcare and labs in particular—are driving the types of systems that we're choosing. The biggest things we keep hearing from developer clients and even our institutions is that they want an "architecture that gets out of the way.” They want deeper spans, column-free space, and taller floor-to-ceiling heights. Right now, flexibility is key because space is so constrained and real estate is so valuable, especially in urban areas. We have to make buildings which are adaptable for multiple future uses – the same building convertible between labs, classrooms, offices, etc.
Karyn: But those design details can be achieved with wood. So I’m wondering if urban design trends, construction practices and experience with wood building materials are influencing architectural choices, especially in multifamily mixed-use developments.
Blake: Certainly there are multifamily housing projects all over the city that use wood. They're all of a certain scale. The further you get from the urban core, the more you start to see wood being used in four-level, multifamily, residential housing projects.
I think the trend for us here in Boston, in particular in the Northeast for sure, is that we've had sort of an aversion to tall buildings. And now we're getting high-rise residential all over the city because real estate values are so high. And I think that's driving the selection of the materials.
Ben: I disagree with Blake there. Our firm has offices in Metro D.C., Pennsylvania, New Jersey and North Carolina. I personally have been involved with several projects in the D.C. area. And we built them out of wood in the urban center. So, they're not just suburban projects.
For example, AvalonBay’s AVA is a six-story building that's concrete podium Type I construction, and then five levels of wood above. It's a crazy dense building for a wood structure.
Honestly, it's just pushing the limits of conventional wood. If we can convince building departments to build an eight-story building out of wood, why not nine? Why not ten? We still hear in public hearings, “You're going to build all that out of wood? That's built to burn!” When in reality once the automatic sprinkler system is installed, it's perfectly safe. Especially with large wood members, they're actually as safe or safer than steel in a fire situation because of the charring of the wood in a fire event creates a natural fire protection layer that can be designed for.
Karyn: So if this isn’t an urban versus suburban question, then how do we start to change the minds of developers and architects about sourcing wood?
Blake: In the Northeast, it may be sustainability. On a lot of the college campuses right now we’re seeing that becoming a big driver for the use of wood. In fact, right now there's this critical mass of Living Building Challenge projects around in Amherst, Mass. And they're all using structural wood, not because of cost or flexibility, but because of the Living Building Challenge’s imperatives associated with material sourcing and biophilia. If we start with the academic clients and we do a Living Building Challenge structure, then we show them, “Hey! This can be done.” Because these aren't just one-off projects for these colleges — they're actually learning how to implement the process so that when they build future structures, they can come in and use the lessons learned. To me, that's how it becomes scalable.
Ben: I actually think the next big thing to drive wood structures is resiliency issues. Developers haven't quite come to grips with what that means. But the question is, how are these buildings that we're designing today going to react in ten, twenty, thirty, forty, fifty years from now with things like rising ocean levels and super storms? That's where we're going next, and wood offers a lot of compelling answers to that question.
Karyn: Good point. As we look toward the future, where does CLT fit into that?
Ben: The key is the code cycle, trying to get enough language modified to bring innovations like CLT into the code. Because where our struggle becomes real is with the building department. That's where we get the red light.
But we’re paying close attention to advancements in CLT and some of those experiments with wood high-rises in Canada, Portland, and New York City.
We really don't see a reason that we couldn't start to do those sorts of things in multifamily construction. The limit is really just the code. When we show up with an eight-story wood building, code officials are already skeptical. So it's going to take more manpower, or political will, or economic factors to justify going higher and to actually get some of the language in the International Building Code to be modified to be a little bit more flexible with these innovative solutions.
And so it’s really just eliminating some of those preconceived notions. And I think CLT and getting one or more of these really provocative wood high-rises built in this country will open up a lot of doors, in terms of the regulations, or just changing the perception of the limits of wood.
Karyn: Where do architects fit into changing those perceptions?
Blake: We have to remember to continue dreaming really big. A lot of times we blame a lack of creativity on everyone but ourselves, but we're just as afraid to be innovative and push the envelope as our clients are sometimes. So I think that we just have to be more convicted and creative and willing to kind of stick our necks out there too.
Ben: That's a good point. Plus, I think we have to start thinking about structures in a new way, too. Because everyone always talks about health, safety and welfare, when what they mean is just safety. But the health and welfare part of it is a big deal, and wood plays into that. There's less embodied energy in wood than in steel or concrete. And it's more recyclable afterwards.
Architects have a responsibility to create healthy spaces for the users of the buildings we design. We don't take that responsibility lightly. The potential to make the world a better place through our projects is real, too. Those projects are connected to clients who are connected to the market, so it does come back to money, sort of—maybe more directly than we would prefer.
But, that's sort of the fun part—when you have these clearly tight constraints and are able to design a project, a space, a building, and a place that serves the population that it was designed for in a profound and thoughtful way. Wood definitely has a role in that discussion.
For more Compelling Conversations with leading architects, visit APA’s Designer Circle website at www.apawood.org/designerscircle.
Karyn Beebe, PE, LEED AP, is an Engineered Wood Specialist for APA – The Engineered Wood Association.
Benjamin Kasdan, AIA, LEED AP, NCARB, is a Director, Design at KTGY Architecture + Planning. He has been involved in the design and planning of a wide variety of real estate projects located throughout California, the East Coast and internationally for more than a decade. Ben’s primary focus is the sustainable design of multifamily, mixed-use, and urban-infill housing developments. He was named one of Building Design + Construction’s 40 Under 40 for 2015.
Blake Jackson, AIA, LEED/WELL Faculty is Sustainability Practice Leader | Associate at TSOI/Kobus & Associates. Versed in all things sustainable, Blake provides multidisciplinary guidance for project teams. Blake was named one of Building Design + Construction's 40 Under 40 for 2015. His international experience, accreditations, and ability to teach add to his status as a firm and design community leader.
About the Author
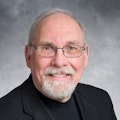