Since the market was reenergized in the mid-2000s, data center owners and clients have been looking to achieve lower first cost and higher quality deployments. First emerging in and around major cities with telecommunications infrastructure, the data center market has since expanded as fiber optic infrastructure has grown and as owners can now utilize more cost-effective land utility power solutions.
The shift to remote locations—whether to serve local client demand or achieve lower first cost and operational costs—has created unique construction obstacles, including the lack of highly-skilled electrical installers available at remote locations. Although remote work may have been a catalyst for modular electrical rooms, many clients are looking to implement these products in major U.S. cities and even overseas.
What's in a Modular Electrical Room?
Modular Electric Rooms (MERs) are prefabricated modular assemblies built out with electrical infrastructure that can be rapidly deployed at a data center facility. MERs support a wide range of equipment with varying contents dependent on the client and their electrical topography.
With shipping constraints and the ability to maintain proper electrical clearances as the major limitation of MERs, MERs are typically approximately 40–60′ long, 14′ wide, 12′ high and support a 1–2 MW electrical lineup in a weatherproof enclosure and contain varying combinations of switchgear, UPS equipment, transformers, and/or battery cabinets. Additionally, there are a wide range of cooling techniques from traditional chilled water, direct expansion equipment, or proprietary systems that may push the envelope of the electrical equipment's environmental requirements.
Even with some limitations, MERs present many prefabrication benefits.
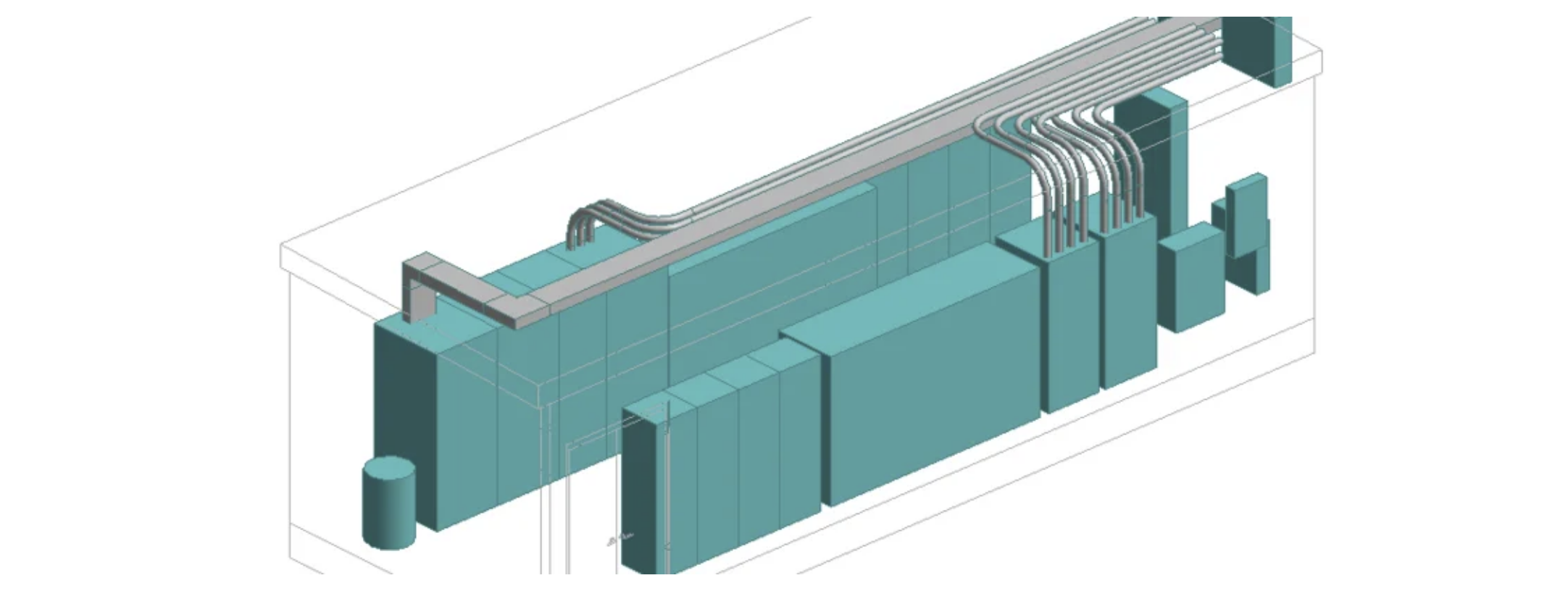
Prefabrication benefits of MERs
Increased productivity in a safer work environment
Fabrication in a shop environment is much faster and safer than field work. When compared to stick-built, the absence of other trades enhances both productivity and safety. Typically, all that is needed onsite is a concrete pad for the new power modules and a pathway to get to the data center. All other work is performed in a controlled shop environment that has been optimized for workflow and safety.
High-quality work that eliminates waste
Repeatable work allows for skilled trade workers to master the MER they're working on in an assembly line-type workflow. This workflow enables them to cut repeatable lengths of conduit and reduce material-handling headaches like excess packaging and boxes. Less variables in the work environment produce a higher quality product, and offsite fabrication also requires less on-site project management and oversight.
Increased speed to market & simplified deployment
One of the most attractive aspects of MERs is the ability to overlap onsite work with offsite MER construction, resulting in a faster finished product and reduced total duration for construction, quality control, point-to-point testing, commissioning, and integration. With a front-end focus on design and procurement, it allows for a simplified deployment of data centers.
Offsite pre-functional testing & commissioning
Once the proof of concept is validated in a factory witness test setting, the manufacturer will be able to produce and reproduce the same product via quality control checkouts, allowing owners to accomplish the majority of electrical, Electrical Power Management System (EPMS), and Mechanical/Building Management commissioning offsite. The offsite testing supports the 'plug and play' mentality and a consistent product drives a more predictable and faster fully integrated systems test or final commissioning checkout.
However, some electrical equipment ratings assume space conditions that have been based on years of interior conditioned installations. Therefore, commissioning parameters may need to be reviewed prior to equipment selection to verify that performance can be met under different environmental conditions.
Scalability
Most owners seek to scale their data centers as the market demand increases or decreases. These pre-engineered systems provide more flexibility to adapt to market needs. If one market sees an increase in demand, while another sees a decrease, owners can deploy and shift resources (MERs) to new locations and increase their data center capacity in response to the demand. The MER 'blocks' make the data center power topology as consistent as possible across multiple sites and can also help support bulk buyout of equipment.
Cost-effective solution
When the process is correctly implemented, the above benefits will be achieved, resulting in lower first cost and higher quality. Prefabrication can reduce electrical first cost, but will often reduce the overall footprint of the electrical gear, allowing more space for data halls and lowering cost/MW.
Success measures
To reach success, extensive project coordination and communication between owners, vendors, engineers, and contractors are critical for success. It's important to avoid targeting unrealistic deadlines or releasing manufacturing too late to ensure the benefits of this process are not lost. Additionally, diversifying supply chains and planning for MER flexibility should be well thought out early in the process to allow the team to transition from one supplier to another based on cost or availability. Any changes based on equipment should be noted for coordination and engineering. Lastly, set expectations early before procurement for factory witness test setup and acceptance criteria.
The emergence of this submarket has pulled design-build contractors and electrical vendors to the forefront. Over the past few years, many producers of premanufactured power modules have emerged as the market has taken off, and many owners have embraced the modularized approach to project delivery and these pre-engineered systems.
As the market demand for these systems across the U.S. grows, MERs continue to offer many positive impacts for projects and data center owners.
More from Author
Southland Industries | Aug 9, 2022
5 Lean principles of design-build
Simply put, lean is the practice of creating more value with fewer resources.
Southland Industries | Dec 20, 2017
6 CFD post-processing tips to improve visualization productivity and quality
Southland Engineering’s Abdullah Karimi offers helpful tips for making computational fluid dynamics (CFD) models more productive.