In the U.S., mass timber has been quickly gaining popularity as a building material—and for good reason. Mass timber can deliver a slew of benefits, chief among them the environmental impact. A renewable alternative to concrete and steel, mass timber can store vast amounts of carbon.
“Mass timber literally grows on trees. When paired with sustainable forestry practices, mass timber has a strong sustainability story,” says Denis Blount, Associate Principal with Arup.
The potential benefits don’t end there.
With a high strength-to-weight ratio, mass timber’s light weight means lower foundation costs. Prefab mass timber components require fewer onsite workers. The material has the potential to create a competitive edge in the marketplace.
And then there’s the undeniable aesthetic appeal of exposed wood, with studies showing its positive impact on wellbeing. “People like the feel of wood, and its visual, tactile nature can provide benefits to occupants,” Blount says.
While mass timber has been used in Europe for decades, more U.S. project teams have been embracing the highly durable material, most commonly in the form of cross-laminated timber (CLT). That’s been propelled partly by the ICC’s inclusion of taller mass timber buildings in the 2021 International Building Code. As of December 2022, almost 1,700 mass timber buildings for multifamily, commercial, and institutional projects had been constructed or were in design throughout the U.S.
Mass timber’s Achilles heel: acoustics
But for all its advantages, mass timber also has a less-heralded quality: its acoustic challenges. Exposed wood ceilings and floors have led to issues with excessive noise. “Acoustics are somewhat of an Achilles heel for mass timber systems,” says Rose Mary Su, Principal Acoustician at Acentech, an acoustics, technology, and vibration consultant based in Cambridge, Mass. Arup’s Blount adds, “I don’t think mass timber necessarily leads to poor acoustics, but it is an inherent challenge.”
To help overcome this obstacle, here are five sound-related problems with mass timber and their solutions:
Problem #1: Wood has less mass than concrete and steel, and that means sound can travel through wood more easily.
While wood’s light weight can help lower construction costs, it also means that mass timber doesn’t deliver the same sound and vibration isolation as concrete or steel. The more mass and density, the better the acoustics. A more massive material such as concrete does better at blocking the transfer of sound. “Whenever you don’t have enough mass, sound goes through the structure,” Su says.
Solution: Add more mass to the mass timber. The reality is that, because of inadequate acoustic performance, completely bare mass timber floors, walls, and ceilings are rare. “You have to do something additional to the timber structure to improve the sound-isolation performance. Add elements, layers, or design features over the base timber structure,” Blount says.
These elements include a poured concrete or gypsum-based layer on top of the floor, in addition to resilient floor underlayments, typically between the topping and the wood. Plus, with a sound-insulated floor, the beautiful wood on the ceiling side can be left exposed.
“Almost all mass timber buildings have additional material like concrete or gypcrete,” says Chris Pollock, Associate Principal, Americas Technical Services Leader, Arup. “Resilient underlayments have a significant benefit for mitigating footfall noise and a marginal improvement to airborne sound separation.”
Arup took this approach on the 80 M Street SE (80 M) project, a vertical extension on top of an existing office building in Washington, D.C. Arup used what Blount calls “a mass timber sandwich”: a mass timber floor with a concrete topping and an underlayment. “We were able to design a structural system that performed well acoustically using a concrete topping,” Blount says.

Problem #2: A concrete or gypcrete layer helps with the noise—but also covers up the wood.
“It’s pretty easy to achieve sound isolation by putting materials on top of mass timber,” Blount says. But the timber-concrete composite technique also obscures the wood—detracting from one of mass timber’s main draws.
Solution: Cover the wood with more wood. Even if they use a concrete or gypcrete layer on the floors, some project teams bring back the timber aesthetic by incorporating more wood elements and decorative pieces into the design. “Add wood details that have sound-absorption finishes to hide the fact it’s not mass timber,” Su says.
As acoustic consultant, Acentech used wood-based, sound-absorbing finishes for the John W. Olver Design Building at the University of Massachusetts in Amherst, the first CLT academic building in the U.S.
Problem #3: Impacts and vibrations come down from the unit above.
It’s not only sound that travels through wood. “A lot of times when people tell us they can hear noise, it’s not just voices traveling through the material, it’s also impact such as footfall,” Su says. This can be especially true of commercial buildings, which don’t have the same sound-related code requirements as residential construction, Su adds.
Solution: Add air space as a buffer. Air space can serve as a sound buffer, reducing both airborne and floor sounds. Air space can be created, for instance, with a drop ceiling or with a floating, engineered-wood floor on top of the floor pad.
Modular units have the advantage of built-in air space between the units. Arup provided the acoustic and fire design services for a multifamily affordable housing project designed for Forterra, a Seattle-based land conservancy. In the project’s apartment module prototype, Arup built an acoustic layer on top of the floor with a topping and an underlayment.
“What’s really nice about modular construction is the stacked modules have air space with insulation material between them, which is good both acoustically and from a thermal protection standpoint,” Blount says.
Problem #4: Some commercial tenants make more noise than others, noise that’s easily transmitted through wood.
Consider the sounds and vibrations generated by a fitness center. Every time someone jumps up and down or drops a weight, that action transmits sound and vibration that travels through a mass timber system, even a concrete-wood composite.
Solution: Consider where you place the spaces and tenants that generate—and are most sensitive to—sound and vibration. The ground floor generally has fewer sound and vibration issues. Often, mixed-use building owners want to dedicate this valuable real estate to the lobby or retail. But they might consider giving at least part of the ground floor to sound-generating amenities, such as gyms, and sound-sensitive tenants, such as labs with expensive equipment. Occupants with fewer noise and vibration sensitivities, such as offices, could be placed in the floors above.
Building materials can certainly help address acoustic issues, but so does a little thoughtful space planning. “Planning is important, and it’s cheaper than trying to solve acoustic challenges after the fact,” Su says.
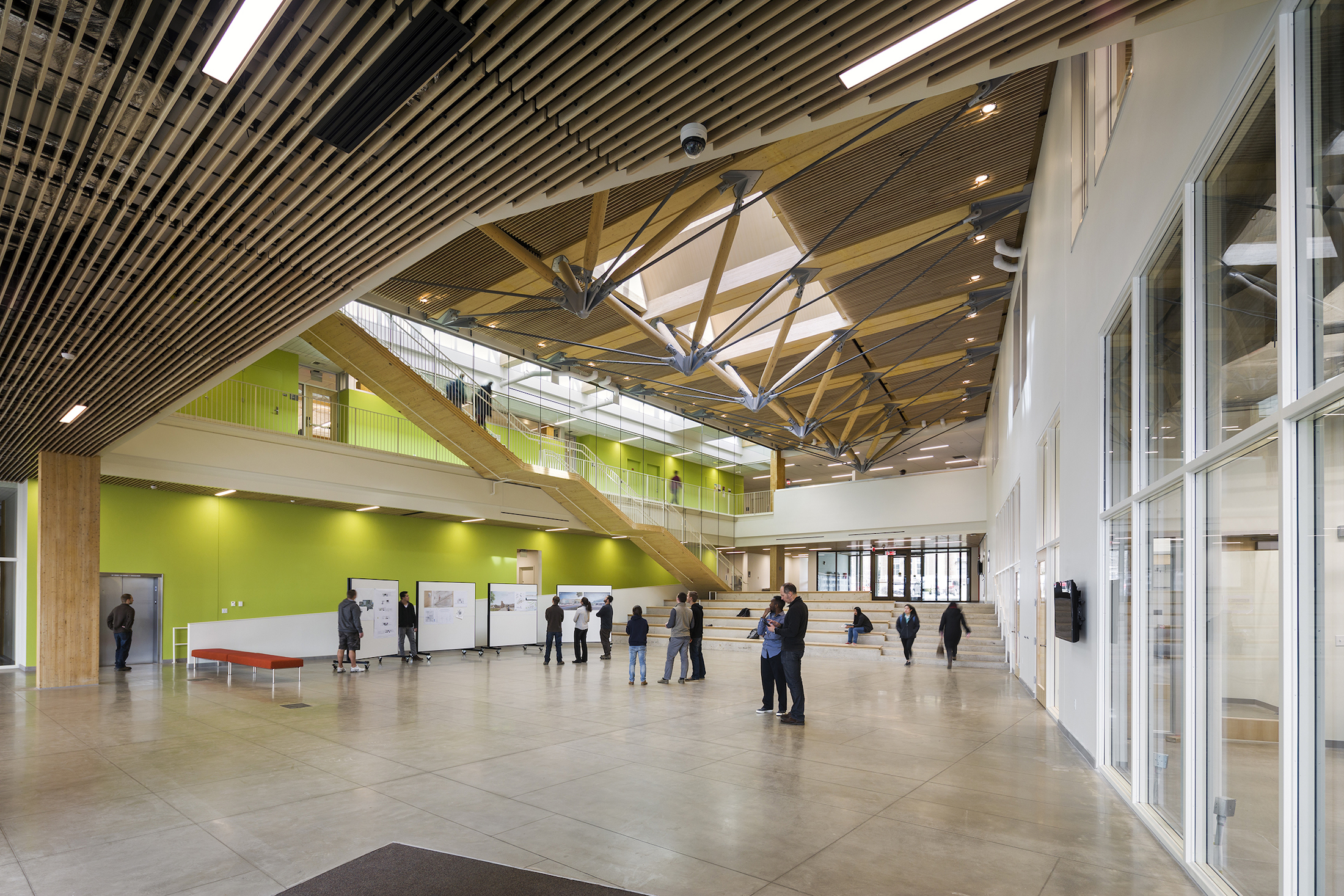
Problem #5: It’s difficult to know the acoustic issues a mass timber project might have until it’s already built.
Given the potential acoustic headaches, builders and developers might reasonably hesitate at using mass timber, especially since it’s still a fairly nascent material in the U.S.
Solution: Step inside a sound or motion simulation. Arup creates acoustic simulations of the sound experiences inside buildings, prior to construction.
“It’s a sonic version of a visual rendering, so we can demonstrate how spaces will sound before they’re built,” Blount says. An acoustic model allows clients to experience what it will sound like, for instance, when someone plays a TV or stereo next door.
Similarly, a motion platform simulates the movement and vibration an occupant will feel inside a structure. So you can experience, for example, what it will feel like when someone walks past your office desk. For the 80 M project, the owner sat inside Arup’s motion platform to feel the vibrations of a timber building as compared to a concrete building. “This gave the owner confidence they would get a subjectively equivalent performance,” Blount says.
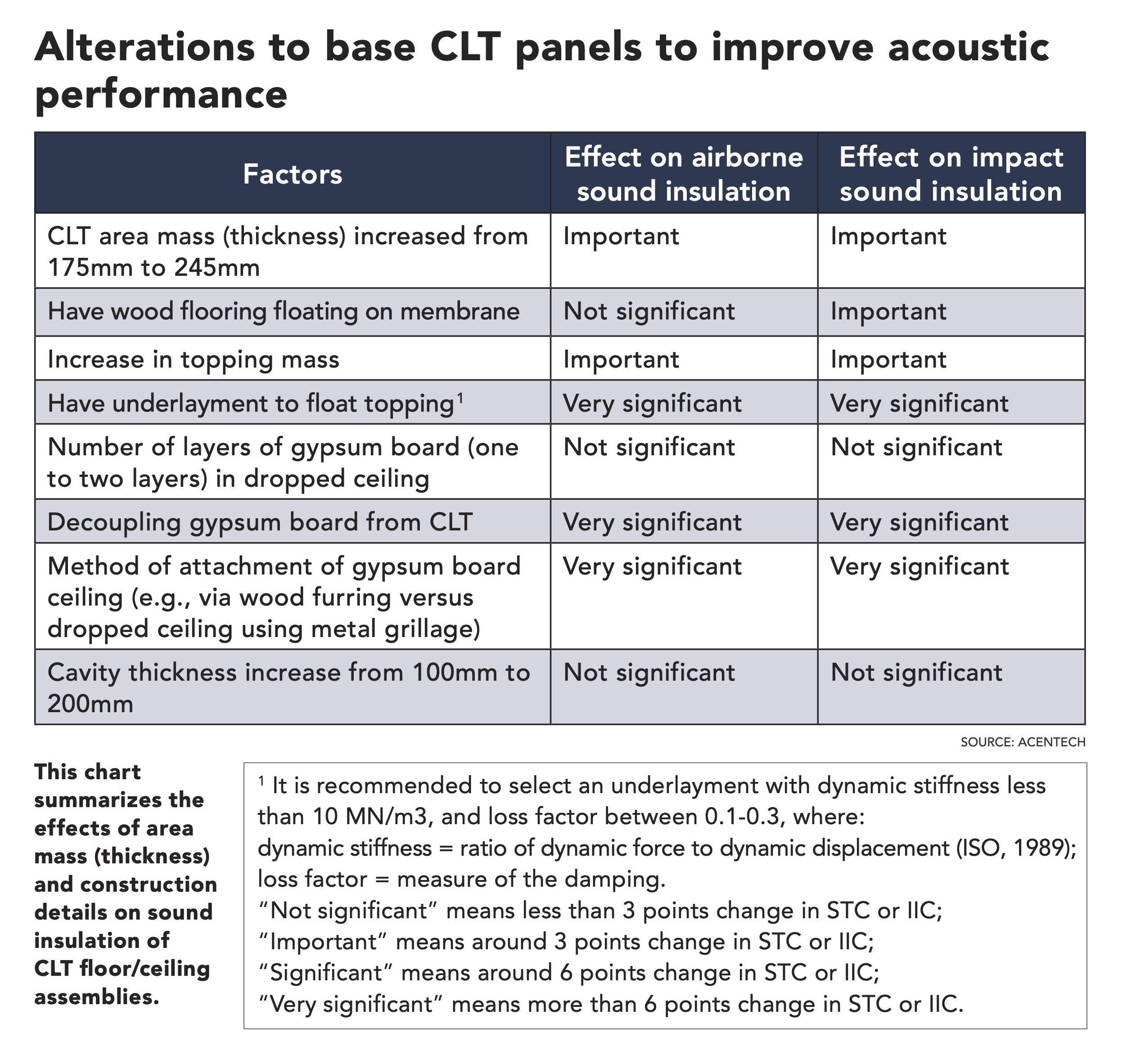
Still the Early Days of mass timber
Looking ahead, acoustic experts say they would like to see more mass timber products that integrate sound absorption techniques. For now, options are limited. StructureCraft produces a dowel-laminated timber (DLT) that places fibrous insulation inside grooves in the wood to absorb sound. “Whether it’s perforations or air pockets or openings, these all could potentially absorb sound or soften the reflection of sound,” Pollock says.
“We’d love to see materials that integrate sound absorption with the ability to expose the beauty of the wood,” Blount says. “We can build all-wood structures, but we still end up using some cementitious material like gypcrete or concrete to improve sound isolation. I’d love to see us replace that with more sustainable material that has better embodied carbon and a lower carbon footprint.”
For mass timber, it’s still early days yet—so there’s plenty of innovation to be done. “Mass timber has a reputation for having challenging acoustics, and there are certainly examples out there of timber buildings that don’t perform as well as concrete or steel,” Blount says. “But part of the story is that the mass timber industry is earlier in its journey compared to concrete or steel. And that leaves a lot of room for innovation.”
Related Stories
Mass Timber | May 8, 2024
Portland's Timberview VIII mass timber multifamily development will offer more than 100 affordable units
An eight-story, 72,000-sf mass timber apartment building in Portland, Ore., topped out this winter and will soon offer over 100 affordable units. The structure is the tallest affordable housing mass timber building and the first Type IV-C affordable housing building in the city.
Mass Timber | Apr 25, 2024
Bjarke Ingels Group designs a mass timber cube structure for the University of Kansas
Bjarke Ingels Group (BIG) and executive architect BNIM have unveiled their design for a new mass timber cube structure called the Makers’ KUbe for the University of Kansas School of Architecture & Design. A six-story, 50,000-sf building for learning and collaboration, the light-filled KUbe will house studio and teaching space, 3D-printing and robotic labs, and a ground-level cafe, all organized around a central core.
Libraries | Apr 24, 2024
New mass timber Teddy Roosevelt library aims to be one with nature
On July 4, 2026, the Theodore Roosevelt Presidential Library is scheduled to open on 93 acres in Medora, a town in North Dakota with under 130 permanent residents, but which nonetheless has become synonymous with the 26th President of the United States, who lived there for several years in the 1880s.
Mass Timber | Apr 22, 2024
British Columbia changing building code to allow mass timber structures of up to 18 stories
The Canadian Province of British Columbia is updating its building code to expand the use of mass timber in building construction. The code will allow for encapsulated mass-timber construction (EMTC) buildings as tall as 18 stories for residential and office buildings, an increase from the previous 12-story limit.
Mass Timber | Mar 17, 2024
Timberlab to build its first mass timber manufacturing plant
The facility anticipates continued demand growth.
Mass Timber | Feb 21, 2024
The future of mass timber construction will depend on codes, costs, and climate change
Hines and DLR Group are moving forward on multiple projects using engineered wood.
Mass Timber | Feb 15, 2024
5 things developers should know about mass timber
Gensler's Erik Barth, architect and regional design resilience leader, shares considerations for developers when looking at mass timber solutions.
Mass Timber | Jan 2, 2024
5 ways mass timber will reshape the design of life sciences facilities
Here are five reasons why it has become increasingly evident that mass timber is ready to shape the future of laboratory spaces.
Airports | Dec 4, 2023
4 key innovations and construction trends across airport design
Here are some of the key trends Skanska is seeing in the aviation sector, from congestion solutions to sustainability.
Mass Timber | Oct 27, 2023
Five winners selected for $2 million Mass Timber Competition
Five winners were selected to share a $2 million prize in the 2023 Mass Timber Competition: Building to Net-Zero Carbon. The competition was co-sponsored by the Softwood Lumber Board and USDA Forest Service (USDA) with the intent “to demonstrate mass timber’s applications in architectural design and highlight its significant role in reducing the carbon footprint of the built environment.”